Other MachineOther Machine
K1C
Manual High-speed Small-hole Drilling EDM
The most reliable and the best selling Small-hole Drilling EDM
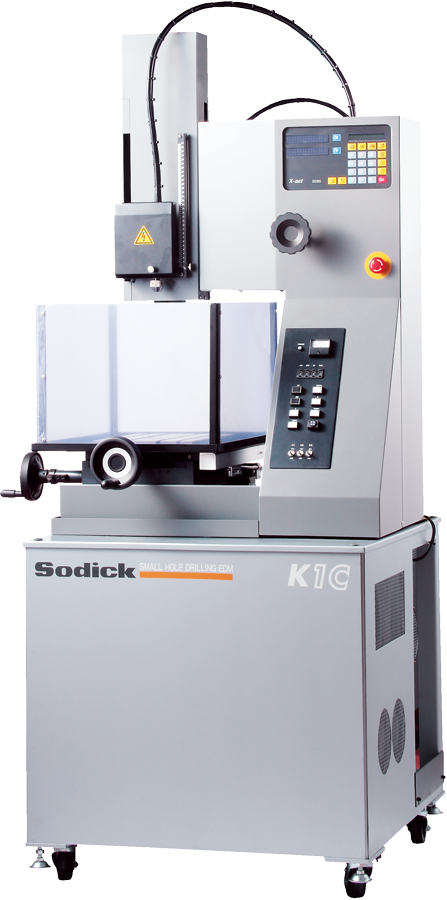
Main Features
The cutting edge servo technologies
Thanks to the latest servo technologies achieved through the know-how accumulated through the development of small hole drilling machines, axis response to the servo command has been greatly improved. Compared with the previous model, two times faster machining speed has been made possible.
Micro-step axis feed
Because axis feed is controlled with micro-level precision, stable and reliable machining is ensured.
Abundant machining conditions
To meet wide range of machining needs, abundant machining conditions have been prepared to cover the combination of various types of electrodes and workpiece.
■ Material:SKD11, Cemented carbide, Aluminum, Copper, SUS, Gr
■ Thickness:10, 20, 50, 100 mm
■ Electrode dimeter:φ0.25, 0.3, 0.5, 1.0, 2.0, 3.0 mmUser friendly design An operation panel was placed on the front of the machine tool for an operator to work with it more comfortably. Display was placed in line with an operator’s eye level. Tool tray was installed in the front of the machine to put dies, electrodes, and etc.
Product Specifications
Technical Specifications | |
---|---|
Axis stroke X x Y x Z (mm) | 200 x 300 x 300 |
Table size W x D (mm) | 250 x 350 |
Max. workpiece weight (kg) | 100 |
Machine tool dimensions W x D x H (mm) | 810 x 870 x 2015 |
K3HS
Ultra High-speed /Small-hole Drilling EDM/with De-ionized Water
Realized continuous automatic high quality & high-speed hole machining for the automobile industry, medical equipment, and electrical & electronic industries.
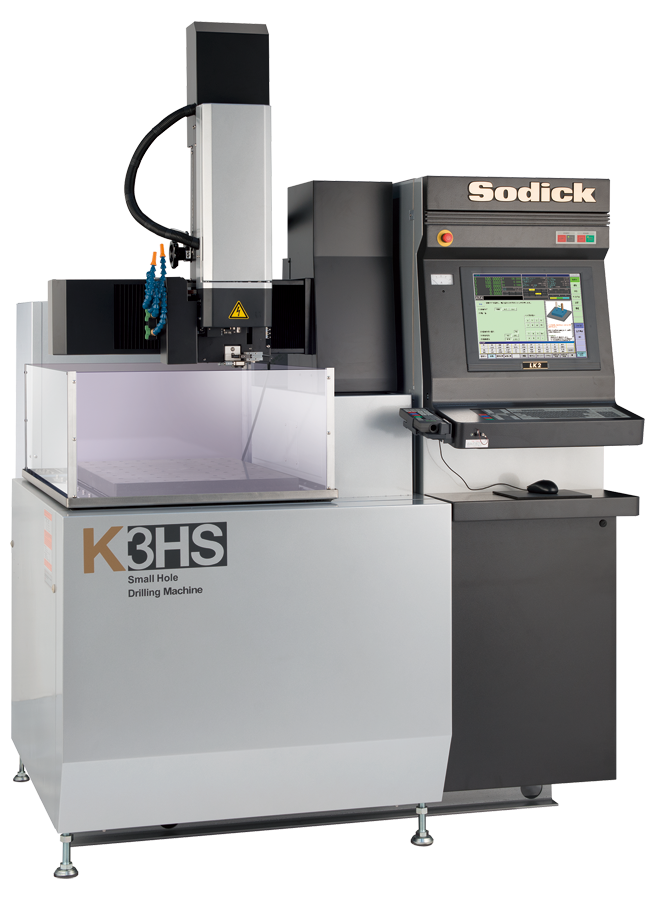
Main Features
Ultra High-speed Machining
Standardly equipped Sodick Motion Controller (K-SMC) realizes optimal servo control. Accordingly, ultra highspeed small hole machining is now possible. While ensuring a spacious machining space, realized a spacesaving design. Equipped with machining conditions including small diameter hole machining by CU pipe electrode and BS (brass) pipe electrode.
Equipped with Latest LK2 Power Supply
Equipped with electric discharge power supply LK2, which enables burr-less and electrolytic corrosion-less in a de-ionized water dielectric fluid. Equipped with various machining conditions for steel, cemented carbide, copper, and aluminum.
Workability and Operability
Standardly equipped with automatic programming software "LN Assist" dedicated to small hole EDM drilling machines, so that machining can also be performed easily even by beginners. Also standardly equipped with Sodick's unique automatic electrode feeder AEF and through hole detection function. Various options are available according to the machining needs, including a high column specification.
Product Specifications
Technical Specifications | |
---|---|
Axis stroke X x Y x Z (mm) | 300 x 400 x 300 |
Table size W x D (mm) | 480 x 790 |
Max. workpiece weight (kg) | 300 |
Machine tool dimensions W x D x H (mm) | 1495 x 1290 x 2150 *1 |
*1 1495×1289×2350:Optional High Column Specification 200 mm |
K1BL
CNC Very-small-hole /Drilling EDM
High response of linear motor drive which realizes continuous and high-precision drilling EDM of very small holes
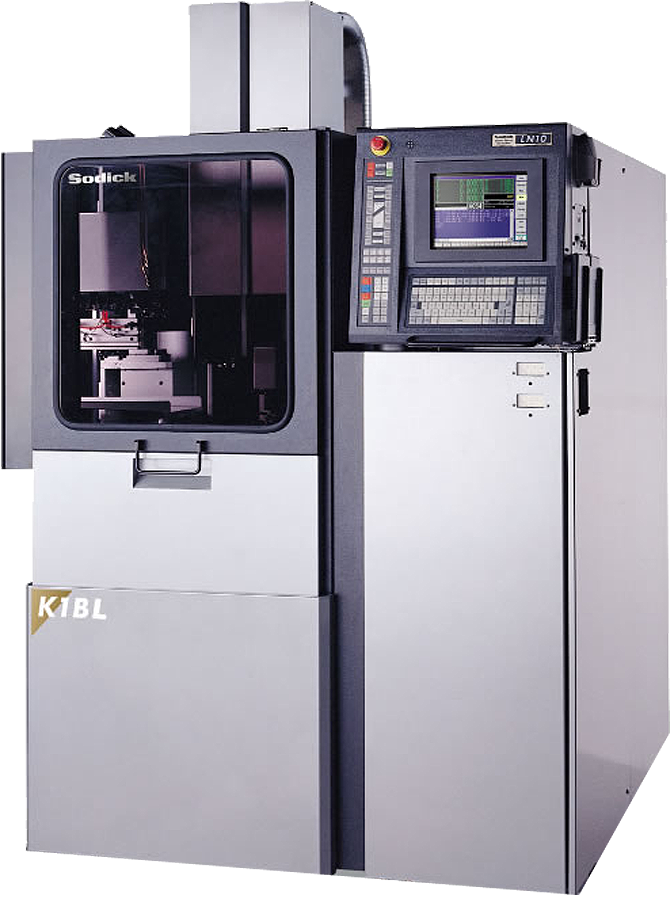
Main Features
Linear motor provied on main axis
A high-speed, high-response linear motor provided on Z axis expands the machining range, stabilizes the operation and reduces the electrode wear.
High-rigidity double-column structure
A high-rigidity double-column structure has been adopted to enable drilling EDM of very small holes. The structure, wherein a column is held by two struts, secures good resistance to thermal deformation and high rigidity, remarkably enhancing machining accuracy.
Automatic electrode changer (AEC)
An AEC provided for this model changes electrodes reliably to facilitate long and continuous drilling EDM of many holes.
Product Specifications
Technical Specifications | |
---|---|
Axis stroke X x Y x Z (mm) | 120 x 150 x 300 |
Table size W x D (mm) | 200 x 250 |
Max. workpiece weight (kg) | 50 *1 |
Machine tool dimensions W x D x H (mm) | 1600 x 1530 x 2305 |
External dimensions (W x D x H, mm) | 900 x 500 x 1620 |
Dielectric fluid | Oil |
Capacity (l) | 172 |
Filtration method | Replaceable paper filter (MF-2400) |
Remote controller | Electrode holder set |
Oscilloscope | Oil |
Work light | Electrode holder stand |
*Including jig |
K4HL
New Premium Small Hole Drilling Machine
The K4HL is built by making the most Sodick’s proven know-how with the successful Wire-cut and Sink EDM range to ensure the highest level of accuracy, incorporates Sodick linear motor drives on X, Y and Z axes.
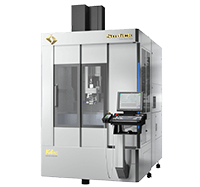
Main Features
Additional options that can be specified for the machine include a rotary table, Automatic Tool Changer (ATC), Lower Guide Changer (LGC), Automatic Electrode Feeder Changer (AEF-C) and a probe unit to measure and adjust the tilt angel of the work-piece.
Product Specifications
Technical Specifications | |
---|---|
Axis stroke X x Y x Z (mm) | 400 x 300 x 500 |
Table dimensions (mm) | 750 x 650 |
Max. workpiece weight (kg) | 500 |
Machine tool dimensions W x D x H (mm) | 1,600 x 2,550 x 3,000 |
External dim. (W x D x H, mm) | 1,250 x 380 x 1,430 |
Weight (empty, kg) | 190 |
Dielectric fluid | De-ionized Water |
Capacity (l) | 140 |
Filtration method | Replaceable paper filter (HF-17) |
Standard Features |
---|
10-year guarantee on positioning accuracy |
Linear Motor (X/Y/Z axis) |
Linear scale (X/Y/Z axis) |
W-axis digital |
Sodick Motion Controller |
Linear motor cooling unit |
Dielectric fluid cooling unit |
LK2 controller |
15“ TFT colour screen |
Remote controller |
LN Professional softwarefor optimum condition search |
Through-hole detection |
Intermediate guides |
AEF (Automatic Electrode Feeder) |
LAN interface |
USB port |
Spindle with max. 1,000 rpm |
Work light |
Options |
---|
Rotary Table |
ATC (Automatic Tool Changer) |
AEF Changer |
LGC (Lower Guide Changer) |
Active Power Restart (UPS) |
8-axis simultaneous control LK20 |
Probe unit |
UH430L
Linear Motor Drive /Ultra High-speed Milling Center
Striving to achieve the ultimate in quality A perfectly balanced all-linear design reflects state-of-the-art advances for the ultimate in high-speed milling.
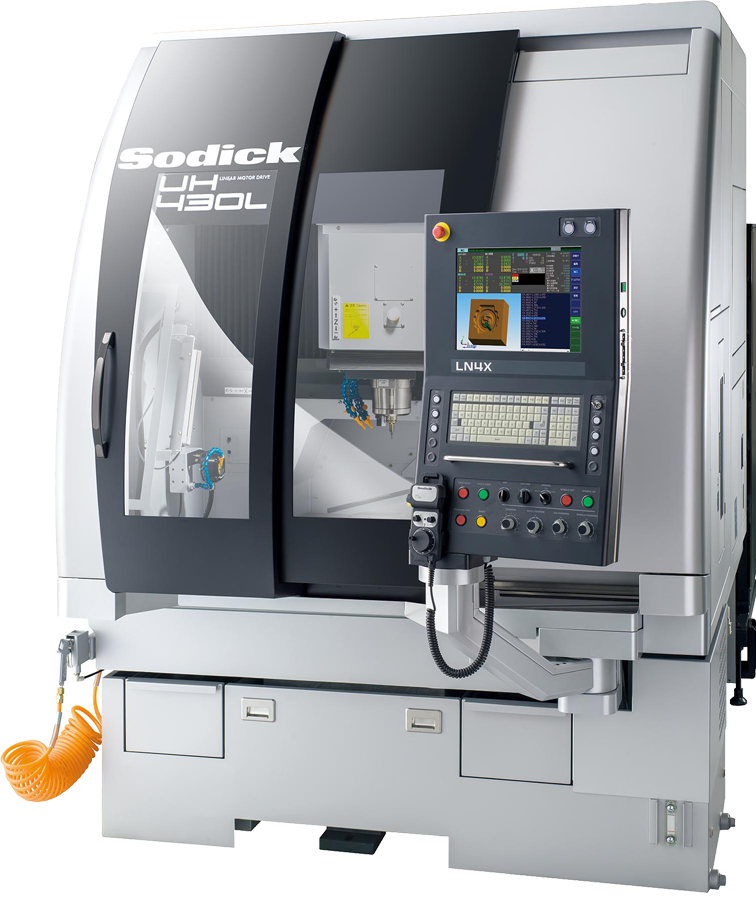
Main Features
A variety of spindles developed in-house
To meet various processing requirements down to the most precise details, you can configure settings by choosing from a lineup of four HSK shrink fit type dual face contact spindles. These spindles suppress vibration and core deflection to provide balance between rotation-torque characteristics and high rigidity.
Incorporates the new and advanced NC unit
Our proprietary motion controller and integrated PWM amplifier improves speed performance for all axes control cycles. We've achieved exceptional improvements in the responsiveness of the driver servos. Improvements to 1 nm* resolution control allow even higher quality finishing achievable at the finest grades.
*1 nm (nanometer) = 1/1,000,000,000 m
The NC operation screen has been refreshed to provide the latest in interface technology, improving visibility and providing a more direct and intuitive operating experience. SEPTune, a new configuration support mode we've developed for the SEPT high-speed and high-precision contour control function, frees you from relying on rules of thumb and enables simple, rapid customization..
Linear Technology from Sodick, the World Leader
Linear motor drives that we’ve developed and manufactured drawing on up to 20 years of experience and knowhow are fitted as standard to each of the three axes. Going fully linear achieves the perfect balance to ensure you get the absolute best in high-precision, high-quality, and high-speed milling.
Product Specifications
Technical Specifications | |
---|---|
Axis stroke X×Y×Z (mm) | 420 x 350 x 200 |
Spindle rotational speed (min-1) | 1500~60000 *1 |
Unit weight (kg) | 6000 |
Total power input (kVA) | 25 |
Machine tool dimensions W x D x H (mm) | 1635 x 3041 x 2205 *2 |
*1 By specification of spindle
*2 Including power supply |
TS50L
Linear Motor Drive Milling Center
X Y Z axis adopt Closed-loop linear motor drive Ensure the long-term stable machining quality
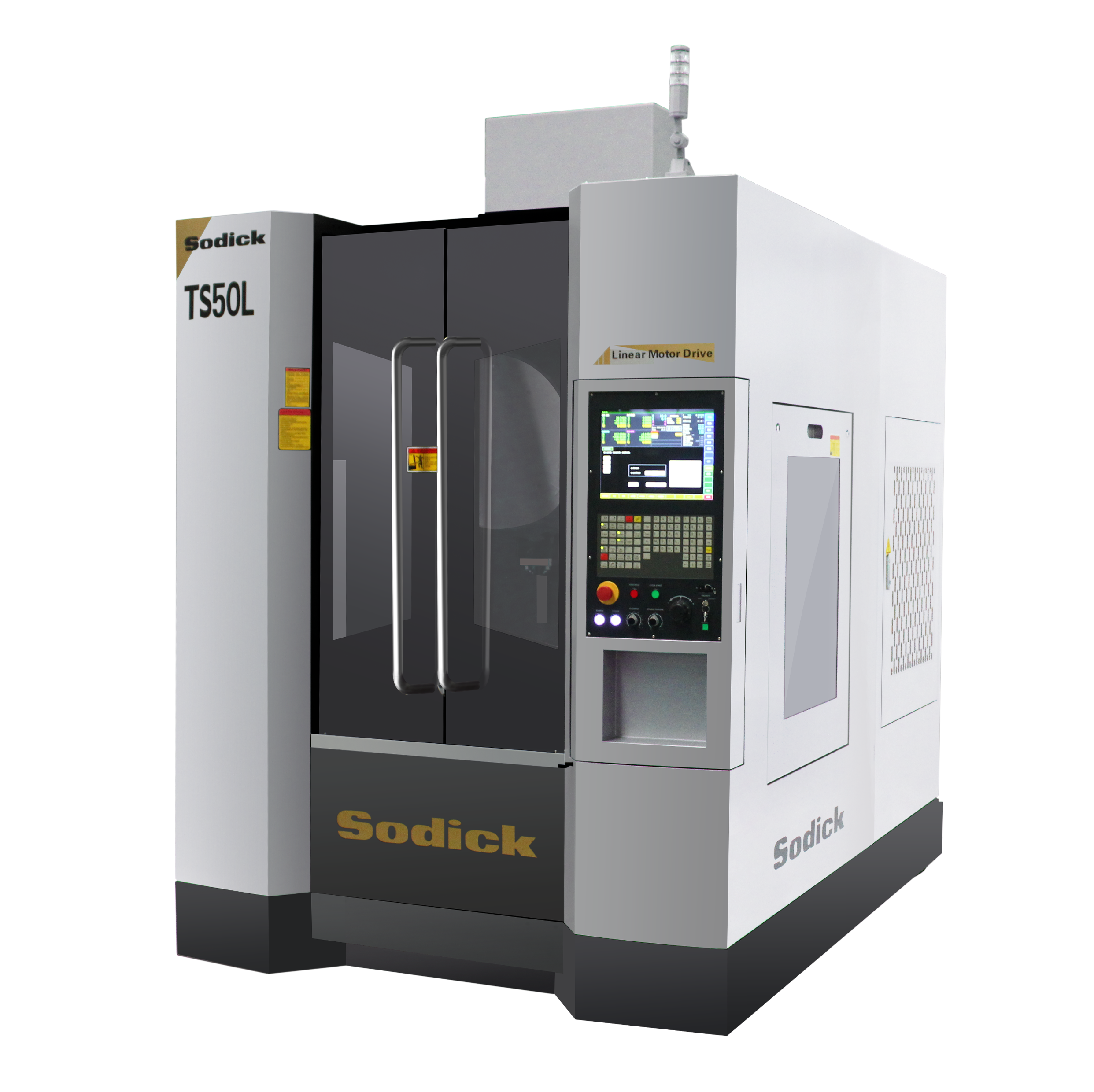
Main Features
Based on experience with linear motor technology over 20 years, Sodick is presenting a new model TS50L Milling center with linear motor drives in all axes to ensure the long term stable machining quality
The simple structure with the magnet plate and coil unit enables assembly without contact, which maintains high repeat accuracy with no wear caused by contact or backlash. Since there is no secular change, stable positioning accuracy and excellent control characteristics of the machining axes can be maintained over a long period.
Product Specifications
Technical Specifications | ||
---|---|---|
Axis travel (X x Y x Z) | 500 x 400 x 300 mm | |
Rapid traverse rate/cutting speed | 40m/min | |
Distance between table top and spindle tip | 150 ~ 450 mm | |
Spindle speed | 18000 min-¹ | |
Tool holder shank | BT30 | |
Maximum tool diameter | Ø 60 mm | |
Machine dimensions (W x D x H) | 1885 x 2615 x 2704 mm | |
Machine tool weight (Including NC Unit) | 3900 kg | |
Table size (X x Y) | 715 x 450 mm | |
Maximum load on table | 200 kg | |
Total power capacity | 20 kva |
Standard Features |
---|
3 Axis Linear Motor Drive |
XYZ Linear scale feedback |
ATC 16 Tools |
Stepdown transformer |
SEPT - Sodick Enhanced Precision Technology |
Ether Net (LAN) |
Work Light |
OPM250L
Linear Motor Drive /Precision Metal 3D Printer
Sodick Linear Motor Drive Precision Metal 3D Printer Provides the One-stop Solution to Customers. Core-technologies for whole Manufacturing process are developed within the Sodick Group.
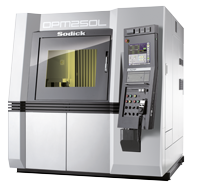
Main Features
One Process Millinge
The one process milling is the fully-automated manufacturing method of whitch Sodick newly propose. The machining enables the continuous process of melting by the irradiation of metallic powder with laser light followed by finish machining by milling with rotating tools. In particular, for die manufacturing for plastic molded products, complex shapes such as three dimensional cooling channels and deep ribs can be manufactured with this single printer.
Linear Motor Drive
The Sodick linear motor drive method is excellent in speed and positioning accuracy, and since there is no mechanical contact, it maintains high responsiveness, stability, maintainability and reliability over long periods. The performance of this linear motor demonstrates maximum performance in combination with the motion controller (K-SMC) which Sodick has developed over the years.
Original NC Unit and CAM
The Sodick in-house developed and manufacturedCNC unit, LN4RP, is used. A die with a built-in three-dimensional cooling channel is designed with CAD and a resin temperature simulation is implemented with CAE. NC programming with dedicated CAM, OS-FLASH, using the designed CAD data is followed by die manufacturing with OPM250L in a one-stop process.
Product Specifications
Technical Specifications | ||
---|---|---|
Max. object size (Width) x (Depth) x (Height) | 250 x 250 x 250 mm | |
X-axis travel | 260 mm | |
Y-axis travel | 260 mm | |
U-axis travel | 260 mm | |
Machining tank internal dimensions (Width) x (Depth) | 290 x 290 mm | |
Spindle Z-axis travel | 100 mm | |
Max. workpiece loading weight | 100 kg | |
Nitrogen supply capacity | 90 NL/min | |
Machine tool dimensions | 1870 x 2230 x 2200 mm (excluding peripheral devices) | |
Machine tool weight | 4500 kg (excluding peripheral devices) | |
Laser type | Yb fiber laser | |
Laser wavelength | 1070 nm | |
Max. laser output | 500 W | |
Laser scanning | Galvano method | |
Max. spindle rotation speed | 6000 to 45000 min-1 | |
Max. spindle torque | 0.8 Nm | |
ATC tool holders | 16 | |
Tool holder system | Dual-contact shrink fit holder HSK-E25 |
|
Control axes | 6 axes (X, Y, Z, U, B, Spindle) | |
Simultaneous control axes | Max. 4 axes | |
Minimum input command | 0.1 μm | |
Minimum drive unit | 0.031 μm | |
OPM ULTRA1 (Maraging Steel) | ||
OPM SUPER STAR (SUS420J2) | ||
OPM Stainless 316 | ||
OPM Stainless 630 |
Options |
---|
MRS unit |
3-light signal tower |
External transformer |
100 VAC outlet |
Air dryer (primary side) |
Air tank |
Material-restricting bellows (rectangular type) |
3-phase input cable |
Shrink fitting device (Heat Robo) |
Base master |
Point master |
Set of pin cushion parts |
Power sifter (unneeded when using MRS unit) |
Sifter (unneeded when using MRS unit) |
Sifter tray lid set (unneeded when using MRS unit) |
Laser eye protection |
Filter replacement dust mask |
Filter replacement dust mask filters |
Tool cutter |
Demagnetizer |
Magnetic flux density meter |
Vertical probe (for magnetic flux density meter) |
Industrial vacuum cleaner (for metallic powder; |
unneeded when using MRS unit) |
Silent cleaner (for fume cleaning) |
High-power cleaner (for floor cleaning) |
Initial processing tool set |
Laser inspection |
USB memory |
Large container (for fume collector cleaning) |
OPM350L
Linear Motor Drive /Precision Metal 3D Printer
Meets Large Size and Diverse Needs. Parallel Mode Significantly Increases Printing Speed. Material Recovery System(MRS:option) Enables Automated Continuous Operation
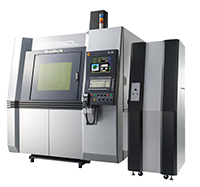
Main Features
One Process Millinge
One-process milling machining is a new fully automated machining method which Sodick proudly proposes. The machining enables the continuous process of melting by the irradiation of metallic powder with laser light followed by finish machining bay milling with rotating tools. In particular, for die manufacturing for plastic molded products, complex shapes such as three dimensional cooling channels and deep ribs can be manufactured with this single printer.
High-Speed Printing and Cutting Time Reduction Material Recovery System
The new machining method (parallel mode) can print multiple spots simultaneously by controlling a single laser source at high speed. Cutting machining time can be reduced significantly by optimizing the balance of lamination count by laser and cutting finish machining with tools depending on the three-dimensional shape to be machined. Continuous operation has been enabled by developing an optional Material Recovery System (MRS) for metallic powder.
Sodick In-House Made NC Unit and Dedicated CAM
The Sodick in-house developed and manufactured CNC unit, LN4RP, is used along with an in-house developed and manufactured high-performance linear motor. A die with a built-in three-dimensional cooling channel is designed with CAD and a resin temperature simulation is implemented with CAE. NC programming with dedicated CAM, OS-FLASH, using the designed CAD data is followed by die manufacturing with OPM350L in a one-stop process.
Product Specifications
Technical Specifications | ||
---|---|---|
Max size of molding object (W x D x H) | 350 x 350 x 350 mm | |
X axis stroke | 360 mm | |
Y axis stroke | 360 mm | |
U axis stroke | 344 mm | |
Molding tank inner dimensions (W x D) | 390 x 390 mm | |
Spindle Z-axis stroke | 100 mm | |
Max powder supply weight | 300 kg | |
Nitrogen supply capacity | 90 NL/min | |
Machine dimensions (Peripheral equipment not included) |
2020 x 2485 x 2220 mm | |
Machine weight (Peripheral equipment not included) |
5800 kg | |
Laser method | "Yb fiber laser/Yb-Faserlaser | |
Laser wavelength | 1070 nm | |
Max laser output | 500W (1000W Option) | |
Laser scan | Galvano method | |
Max main spindle rotation speed | 45000 min-1 | |
Max main spindle torque | 0.8 Nm | |
Number of tools | 20 | |
Tool holder method | Dual face contact holder HSK-E25/ | |
Control axes | XYZUB, Spindle | |
Simultaneouse control axes | Max. 4 axes | |
Minimum input command | 0,1 μm | |
Minimum drive unit | 0,031 μm |