Wire-cut EDMWire-cut EDM
AL Series “i Groove⁺ Edition”
AL Series “i Groove Edition”
AL Series
VL Series
VN Series
VZ Series
AQ Series
AP Series
AL400P "i Groove Edition" NEW!!
First in the world ! Wire Rotation Mechanism "i groove" Achieves high precision machining while suppressing the cumulative pitch error to the utmost in progressive press dies and etc. where high precision is accelerating
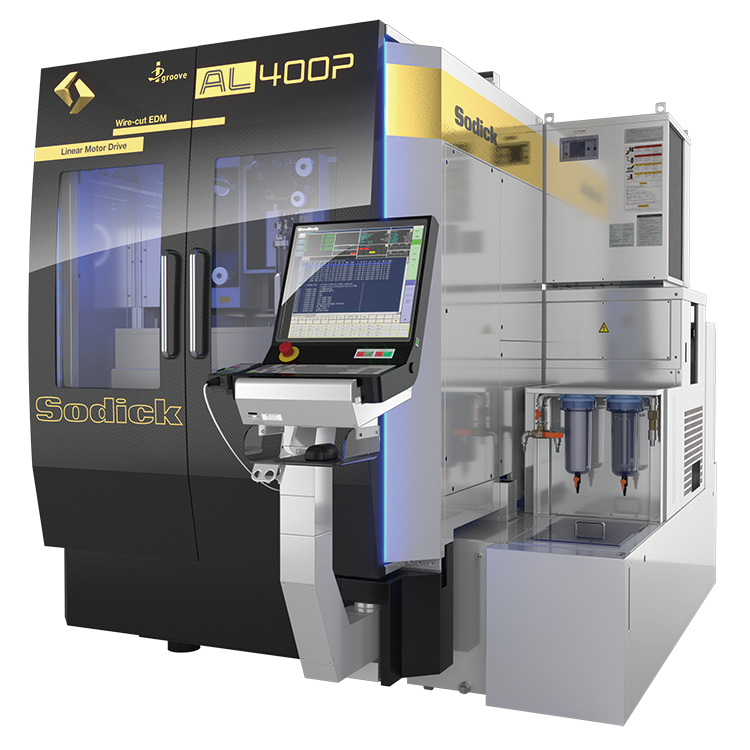
Main Features
More efficient and environmentally friendly finishing of thick plate workpieces.
- Wire Rotation Mechanism "i groove" -
Applying rotation to the wire during finishing reduces wire consumption and allows a new wire surface to be constantly used for finishing from the top to the bottom of the workpiece.
This is especially suited to finishing thick plate workpieces.
It offers innovative machining performance including stable machining dimensions, improvement of surface scoring, and reduced wire consumption.
- New groove and step machining function "Stepcut" -
It permits machining at the same speed as under standard conditions while significantly improving the accuracy and range of applications when machining shapes with rapidly changing material thickness, such as stepped shapes.
Latest Electrical Discharge Technology for Rapid and Accurate Machining
Sodick has been working for many years to develop the world's best wire-cut electric discharge machines. The AL Series "i Groove Edition" offers flexible control from high peak currents for efficient rough machining to ultra-fine discharge pulses for micro finishing.
In addition, The Sodick linear motor drive is a non-contact system that eliminates the need for ball screws. It is maintenance-free and maintains its initial accuracy almost indefinitely, with no drop off in machine accuracy due to ball screw wear throughout the life of the machine (10 years or more).
High Precision Premium Specification, Pursuing Ultimate Accuracy
Sodick pursued ultra-high precision in the machining, assembly and adjustment of machinery. By adopting ultra-high precision roller guides, high rigidity was also achieved.
While standardly equipped with doors made of CFRP, the accuracy was thoroughly pursued in all factors originating in the machining accuracy to temperature control by a high quality inverter cooler.
Product Specifications
Machine Tool | |
---|---|
X - Axis Travel (mm) | 400 |
Y - Axis Travel (mm) | 300 |
Z - Axis Travel (mm) | 250 |
Work Tank Inner Dimensions (W x D) (mm) | 850 x 610 |
U x V Axis Travel (mm) | 150 x 150 |
Max. Taper Angle (W x D x H) | 600 x 470 x 240 (Flush Machining) 600 x 470 x 230 (Immersion Machining) |
Max. Weight of Workpiece (kg) | 500 (Flush Machining) 350 (Immersion Machining) |
Wire Diameter (mm*1) | ø0.05 to ø0.3 |
Wire Tension | 3 to 23 N |
Max. Wire Feed Speed | Max. 420 mm/sec |
Distance from Floor to Table Upper Surface (mm) | 995 |
Total Electric Capacity | 3-phase 50/60 Hz 13 kVA*2 |
*1 Less than ø0.05 mm to ø 0.1 mm is optional.
*2 Electric capacity when ø 0.2 mm wire is used. |
Dielectric Tank | |
---|---|
External Dimensions (W x D x H) | 775 x 2,250 x 2,202 mm |
Weight (Empty) | 450 kg |
Capacity | 792 liter |
Machining Fluid Filtration Method | Paper Filter Replacement Type (4 Cylinder Inner Pressure Type) |
Demineralizer | Ion Exchange Resin (18 Liter Specification) |
CNC Power Supply SP/SP-E | |
---|---|
Max. Machining Current | 40A (60A : Option) |
Power Supply Input Specification | AC200V 50/60 Hz |
NC Unit | Multi-tasking OS, K-SMC-LINK Method (M4-LINK) |
User’s Memory Capacity | Editing: 100,000 Blocks Saving: 30 M bytes |
Memory Device | SSD, Dedicated USB Memory |
Input Method | Dedicated USB Memory, Multi-touch Panel, Keyboard, LAN |
Display Method | 19-inch TFT-LCD |
Printable Characters | Kanji (JIS Level 1 Kanji Characters), Alphabet, Numerical Characters, etc.. |
Keyboard | Standard 101 Keyboard, Function Key |
Position Command Method | Incremental / Absolute in Combination |
Input Range | ±999999.999/±99999.9999 /±9999.99999/±999.999999 (Changeable) |
Electric Discharge Machining Condition Registration Function |
10,000 conditions can be registered (C0000 to C9999) |
Offset Function | 10,000 conditions can be registered (H0000 to H9999) |
Program Sequence Number Specification | Setting from N000000000 to N999999999 |
Coordinate Value | 60 |
Number of Simultaneously Controlled Axes | 4 Axes Max (SPW-E: 8 Axes Max *3) |
Min. Command Unit | 0.001μm |
Min. Drive Unit | 0.01μm (X, Y, U, V Axes) |
Max. Feed Speed | X, Y-axis: Max. 3 m/min, Z-axis: 2 m/min |
Position Detection Method | Full Closed Loop (Linear Scale) |
Drive System | Linear Motor (X, Y, U, V Axes) |
Drive Mechanism | Linear Motor |
Various Compensation | Pitch Error, Plane Pitch Error, Torque and Torsion Compensation for Each Axis. Workpiece Inclination and Workpiece Distortion Compensation. |
Graphics Function | XY, YZ and XZ Planes, Drawing while Machining, Machining Position, 3-dimensional Machining, Zoom In, Zoom Out, Rotation, Background Drawing, etc. |
*3 SPW-E maximum of 8 axis specification is available for
AL400P/AL400G/ALN400G, AL600P/AL600G/ALN600G. |
ALC400P "i Groove Edition"
Smart Pulse & Smart Linear
Super-accurate Wire EDM
When Sodick set itself the task of improving on the performance and accuracy of its ALC-G series it took on a major challenge – these machines are already technical leaders, incorporating Sodick linear technology and digital Smart Pulse generators. But some sectors have requirements are even more demanding and Sodick was finding that an increasing number of customers were looking for super-high accuracy, for example a pitch accuracy of +/-1 micron – and every element of the ALC-P series has been developed to achieve these objectives.
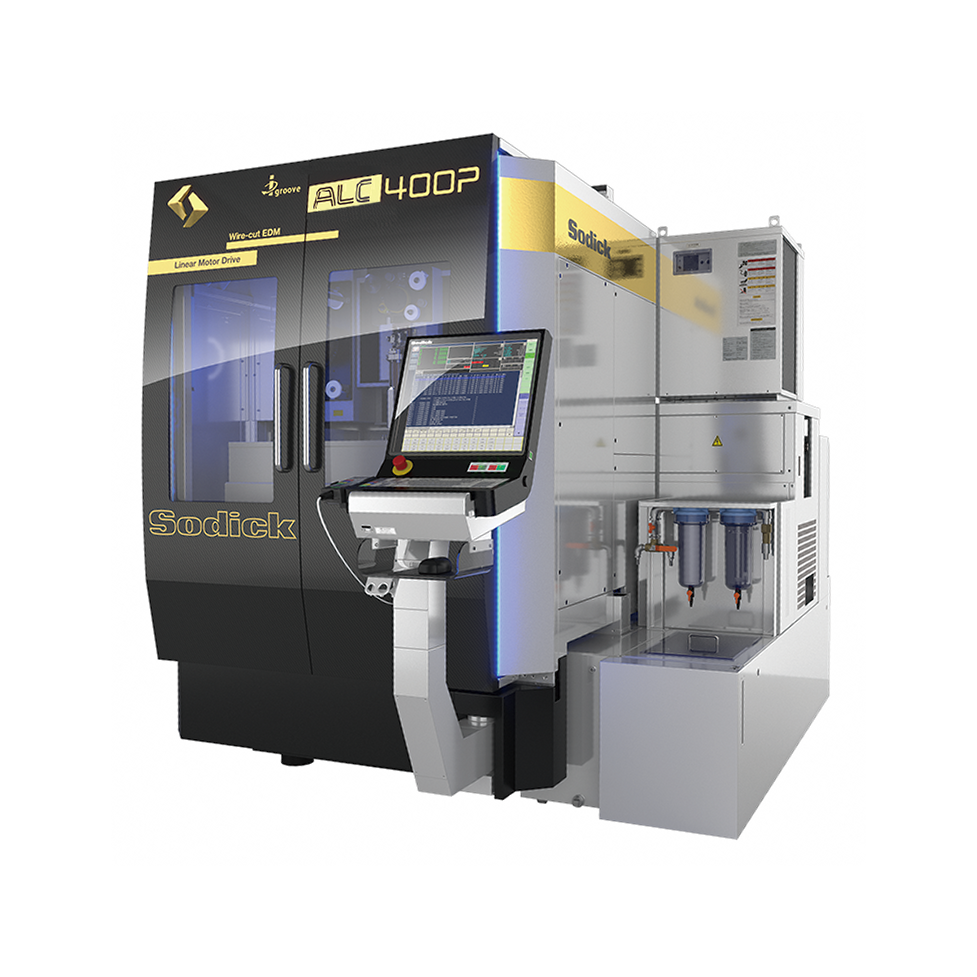
Main Features
New Wire Rotation Mechanism
This newly developed technology, patented by Sodick, rotates the wire during the skim cut operation, so that workpieces are machined from top to bottom with the “unconsumed” surface of the wire.
Conventionally, wire electrodes are controlled solely by tension and running speed, while being constrained by a die. Sodick’s iGroove rotation mechanism provides additional control over the wire, resulting in increased surface quality and improved geometric accuracy, whilst at the same time minimising.
Machine Construction
The machine has a variety of standard built-in functions, including a new tension servo function, auto fluid-level control, and the new FJ-AWT (Automatic Wire Threader). Paying close attention
to the machine accessibility for work preparation in the field, a square-shaped work stand, ceramic stand base, 3-sided machining tank with automatic lifting door, quadruple filters and many
other features, all of which works to ensure improvements in productivity. Furthermore, by adopting a unique full-cover machine structure, comfort and safety in the work environment is not compromised.
Product Specifications
Technical Specifications | |
---|---|
X - Axis Travel (mm) | 400 |
Y - Axis Travel (mm) | 300 |
Z - Axis Travel (mm) | 250 |
Taper angle (Work. thickness 130mm) | ± 25° |
Work tank dimensions (W x D) | 850 x 610 mm |
Max. workpiece weight | 500 kg |
Wire Diameter | 0.1 ~ 0.3 mm |
Wire Tension | 3 ~ 23N |
Max. Wire Speed | 420 mm/sec |
Distance from floor to table top | 995 mm |
Machine tool dimensions (W x D x H) | 2,190 x 2,590 x 2,230 mm |
Machine installation dimensions | 3,425 x 3,850 mm |
Machine tool weight | 3400 kg |
Total power input | 3-phases 50/60Hz 13KVA |
External dimensions (W x D) | 775 x 2,250 mm |
Empty weight | 450 kg |
Capacity | 790 lit |
Dielectric fluid filtration system | 4 Replaceable paper filters internal pressure) |
Deionizer | Ion exchange resin (18-lit. type) |
AL600P "i Groove Edition" NEW!!
Linear Motor Drive /High Speed & High Precision Wire-cut EDM
First in the world ! Wire Rotation Mechanism "i groove" Achieves high precision machining while suppressing the cumulative pitch error to the utmost in progressive press dies and etc. where high precision is accelerating
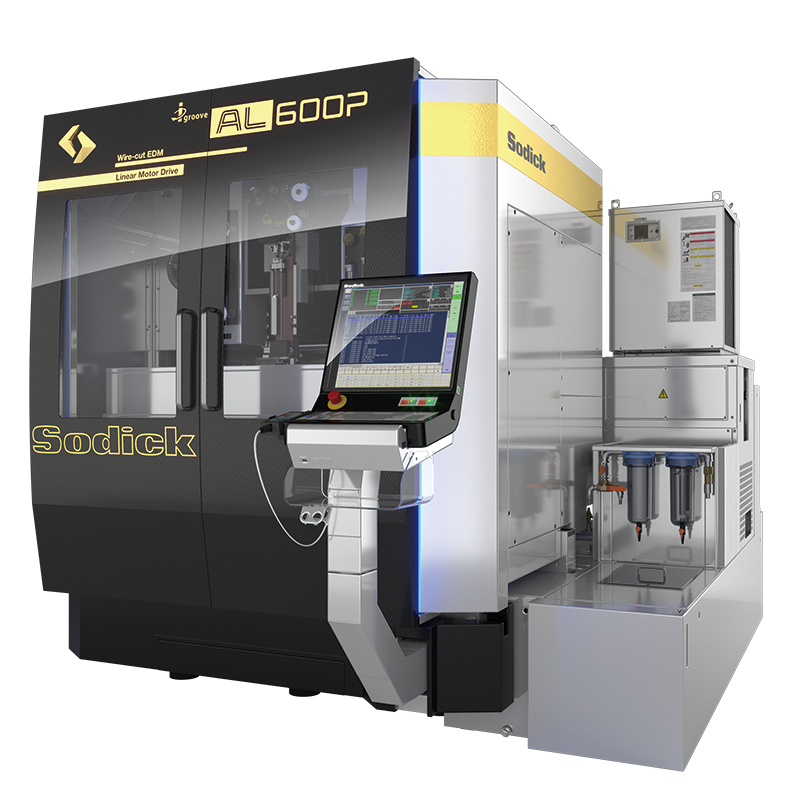
Main Features
More efficient and environmentally friendly finishing of thick plate workpieces.
- Wire Rotation Mechanism "i groove" -
Applying rotation to the wire during finishing reduces wire consumption and allows a new wire surface to be constantly used for finishing from the top to the bottom of the workpiece.
This is especially suited to finishing thick plate workpieces.
It offers innovative machining performance including stable machining dimensions, improvement of surface scoring, and reduced wire consumption.
- New groove and step machining function "Stepcut" -
It permits machining at the same speed as under standard conditions while significantly improving the accuracy and range of applications when machining shapes with rapidly changing material thickness, such as stepped shapes.
Latest Electrical Discharge Technology for Rapid and Accurate Machining
Sodick has been working for many years to develop the world's best wire-cut electric discharge machines. The AL Series "i Groove Edition" offers flexible control from high peak currents for efficient rough machining to ultra-fine discharge pulses for micro finishing.
In addition, The Sodick linear motor drive is a non-contact system that eliminates the need for ball screws. It is maintenance-free and maintains its initial accuracy almost indefinitely, with no drop off in machine accuracy due to ball screw wear throughout the life of the machine (10 years or more).
High Precision Premium Specification, Pursuing Ultimate Accuracy
Sodick pursued ultra-high precision in the machining, assembly and adjustment of machinery. By adopting ultra-high precision roller guides, high rigidity was also achieved.
While standardly equipped with doors made of CFRP, the accuracy was thoroughly pursued in all factors originating in the machining accuracy to temperature control by a high quality inverter cooler.
Product Specifications
Technical Specifications | |
---|---|
Machining Tank Inner Dimensions (W x D) | 1,050 x 710 mm |
X Axis Travel | 600 mm |
Y Axis Travel | 400 mm |
Z Axis Travel | 350 mm |
U x V Axis Travel | 150 x 150 mm |
Max. Taper Angle | ± 25° (Thickness: 130 mm) |
Max. Workpiece Size (W x D x H) | 800 x 570 x 340 (Flush Machining) mm 800 x 570 x 280 (Immersion Machining) mm |
Max. Weight of Workpiece | 1,000 kg |
Wire Diameter | ø0.05 to ø0.3 mm *1 |
Wire Tension | 3 to 23 N |
Max. Wire Feed Speed | Max. 420 mm/sec |
Distance from Floor to Table Upper Surface | 995 mm |
Total Electric Capacity | 3-phase 50/60 Hz 13 kVA*2 |
External Dimensions (W x D x H) | 870 x 2,605 x 2,179 mm |
Weight (Empty) | 500 kg |
Capacity | 1001 liter |
Machining Fluid Filtration Method | Paper Filter Replacement Type (4 Cylinder Inner Pressure Type) |
Demineralizer | Ion Exchange Resin (18 Liter Specification) |
Max. Machining Current | 40A (60A : Option) |
Power Supply Input Specification | AC200V 50/60 Hz |
NC Unit | Multi-tasking OS, K-SMC-LINK Method (M4-LINK) |
User’s Memory Capacity | Editing: 100,000 Blocks Saving: 30 M bytes |
Memory Device | SSD, Dedicated USB Memory |
Input Method | Dedicated USB Memory, Multi-touch Panel, Keyboard, LAN |
Display Method | 19-inch TFT-LCD |
Printable Characters | Kanji (JIS Level 1 Kanji Characters), Alphabet, Numerical Characters, etc.. |
Keyboard | Standard 101 Keyboard, Function Key |
Position Command Method | Incremental / Absolute in Combination |
Input Range | ±999999.999/±99999.9999 /±9999.99999/±999.999999 (Changeable) |
Electric Discharge Machining Condition Registration Function |
10,000 conditions can be registered (C0000 to C9999) |
Offset Function | 10,000 conditions can be registered (H0000 to H9999) |
Program Sequence Number Specification | Setting from N000000000 to N999999999 |
Coordinate Value | 60 |
Number of Simultaneously Controlled Axes | 4 Axes Max (SPW-E: 8 Axes Max *3) |
Min. Command Unit | 0.001μm |
Min. Drive Unit | 0.01μm (X, Y, U, V Axes) |
Max. Feed Speed | X, Y-axis: Max. 3 m/min, Z-axis: 2 m/min |
Position Detection Method | Full Closed Loop (Linear Scale) |
Drive System | Linear Motor (X, Y, U, V Axes) |
Drive Mechanism | Linear Motor |
Various Compensation | Pitch Error, Plane Pitch Error, Torque and Torsion Compensation for Each Axis. Workpiece Inclination and Workpiece Distortion Compensation. |
Graphics Function | XY, YZ and XZ Planes, Drawing while Machining, Machining Position, 3-dimensional Machining, Zoom In, Zoom Out, Rotation, Background Drawing, etc. |
*1 Less than ø0.05 mm to ø 0.1 mm is optional.
*2 Electric capacity when ø 0.2 mm wire is used. *3 SPW-E maximum of 8 axis specification is available for AL400P/AL400G/ALN400G, AL600P/AL600G/ALN600G. |
ALC600P "i Groove Edition"
Smart Pulse & Smart Linear
Super-accurateWire EDM
When Sodick set itself the task of improving on the performance and accuracy of its ALC-G series it took on a major challenge – these machines are already technical leaders, incorporating Sodick linear technology and digital Smart Pulse generators. But some sectors have requirements are even more demanding and Sodick was finding that an increasing number of customers were looking for super-high accuracy, for example a pitch accuracy of +/-1 micron – and every element of the ALC-P series has been developed to achieve these objectives.
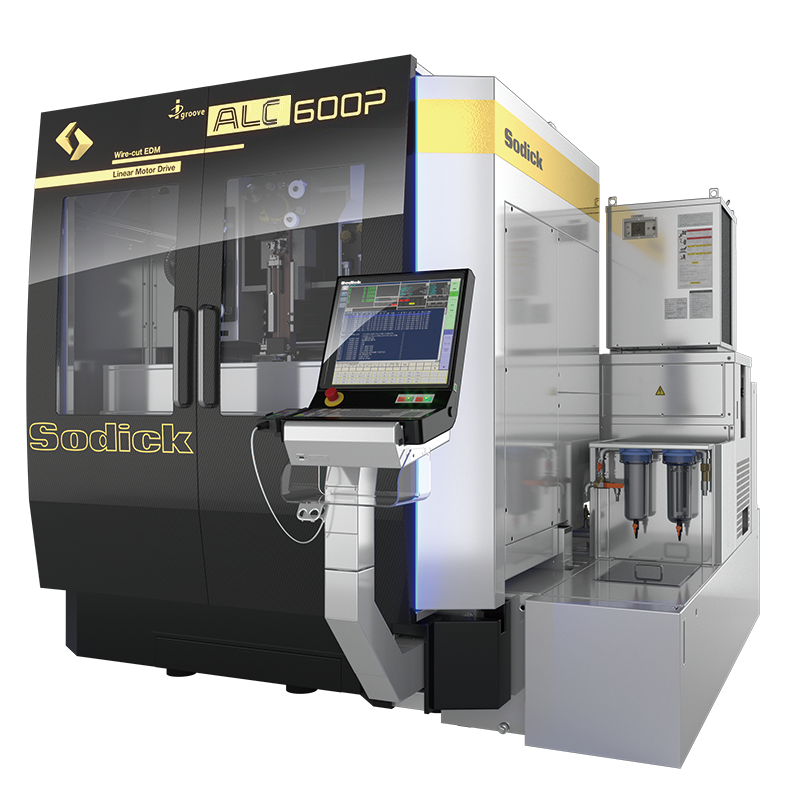
Main Features
New Wire Rotation Mechanism
This newly developed technology, patented by Sodick, rotates the wire during the skim cut operation, so that workpieces are machined from top to bottom with the “unconsumed” surface of the wire.
Conventionally, wire electrodes are controlled solely by tension and running speed, while being constrained by a die. Sodick’s iGroove rotation mechanism provides additional control over the wire, resulting in increased surface quality and improved geometric accuracy, whilst at the same time minimising.
Machine Construction
The machine has a variety of standard built-in functions, including a new tension servo function, auto fluid-level control, and the new FJ-AWT (Automatic Wire Threader). Paying close attention
to the machine accessibility for work preparation in the field, a square-shaped work stand, ceramic stand base, 3-sided machining tank with automatic lifting door, quadruple filters and many
other features, all of which works to ensure improvements in productivity. Furthermore, by adopting a unique full-cover machine structure, comfort and safety in the work environment is not compromised.
Product Specifications
Technical Specifications | |
---|---|
X - Axis Travel (mm) | 600 |
Y - Axis Travel (mm) | 350 |
Z - Axis Travel (mm) | 350 |
Taper angle (Work. thickness 130mm) | ± 25° |
Work tank dimensions (W x D) | 1050 x 710 mm |
Max. workpiece weight | 1000 kg |
Wire Diameter | 0.1 ~ 0.3 mm |
Wire Tension | 3 ~ 23N |
Max. Wire Speed | 420 mm/sec |
Distance from floor to table top | 995 mm |
Machine tool dimensions (W x D x H) | 2,575 x 2,945 x 2,345 mm |
Machine installation dimensions | 3,860 x 4,245 mm |
Machine tool weight | 4,600 kg |
Total power input | 3-phases 50/60Hz 13KVA |
External dimensions (W x D) | 870 x 2,605 mm |
Empty weight | 500 kg |
Capacity | 1000 lit |
Dielectric fluid filtration system | 4 Replaceable paper filters internal pressure) |
Deionizer | Ion exchange resin (18-lit. type) |
AL400G "i Groove⁺ Edition" NEW!!
Linear Motor Drive /High speed & High Performance Wire-cut EDM
Newly developed Digital HF control, wire rotation mechanism, energy-saving pump
Manufacturing that is both "High-speed" and "Eco-friendly" that can be changed digitally
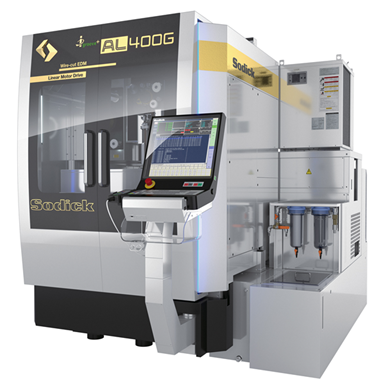
Main Features
4-axis linear motor drive
High-performance linear motors developed and manufactured in-house are used for four axes (XYUV). Precise axis movements without backlash can be maintained semi-permanently.
Demonstrates accurate position control and excellent discharge characteristics while machining, through the high response and high following characteristics which are
the features of the linear motor.
Improved Machining Speed
Newly developed Digital HF control is adopted. By constantly digitally monitoring the status during machining and maintaining optimum discharge conditions, the controller simultaneously
improves machining speed and accuracy. By constantly monitoring the discharge state during machining, stable machining can be maintained at all times, even with changes in water
quality or plate thickness.
Eco-friendly
The wire rotation mechanism (i groove) always performs finish machining with a wear-free wire surface, enabling uniform machining from the top to the bottom of the workpiece.
Reduces wire consumption while reducing streaks and irregularities during finishing of thick workpieces. In addition, a newly developed energy-saving pump system has been adopted
for the dielectric tank, reducing power consumption.
Product Specifications
Technical Specifications | ||
---|---|---|
X - Axis Travel (mm) | 400 | |
Y - Axis Travel (mm) | 300 | |
Z - Axis Travel (mm) | 250 | |
U x V Axis Travel (mm) | 150 x 150 | |
Machining Tank Inner Dimensions W x D (mm) | 850 x 610 | |
Max. Taper Angle | ± 25° (Plate Thickness: 130 mm) | |
Max. Workpiece Dimensions W x D x H (mm) | 600 x 470 x 230 (Submerged) 600 x 470 x 240 (Flushing) |
|
Max. Workpiece Weight (kg) | 500 (350 Submerged) | |
Wire Diameter (mm) | ø0.05 - ø0.3 mm *1 | |
Wire Tension (N) | 3 ~ 23 | |
Maximum Wire Feed Rate (mm/sec) | 420 | |
Distance from floor surface to upper surface of table (mm) | 995 | |
Machine Tool Dimensions W x D x H (mm) | 2,190 x 2,590 x 2,230 | |
Machine Installation Dimensions W x D (mm) | 3,425 x 3,850 | |
Total Unit Weight (kg) | 3,400 | |
Total Power Input | 3-phase 50/60 Hz 13 kVA | |
*1 0.05 to 0.1 mm diameters are available as options. |
ALC400G "i Groove Edition"
Smart Linear, Smart Pulse, Premium
First in the world ! Wire Rotation Mechanism "i groove"
Achieving the superlative performance with in-house developed core technologies.
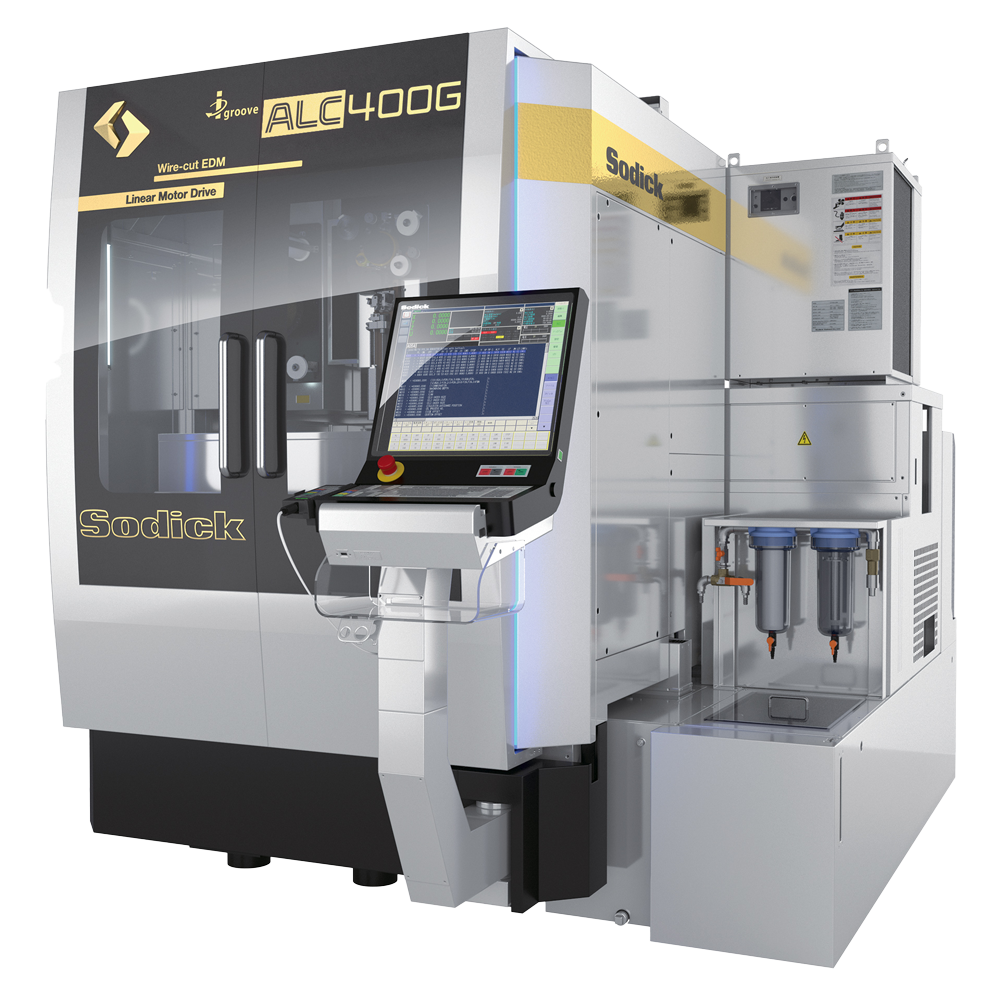
Product Specifications
Technical Specifications | ||
---|---|---|
X/Y/Z axis travel (mm) | 400 x 300 x 250 | |
U/V axis travel (mm) | 150 x 150 | |
Taper angle (Work. height 130mm) | ±25° | |
Work tank dimensions (W x D, mm) | 850 x 610 | |
Max. workpiece weight (kg) | 500 | |
Wire diameter (mm) | Ø 0.1 ~ Ø 0.3 | |
Wire tension (N) | 3 ~ 23 | |
Max. wire speed (mm/sec) | 420 | |
Max. wire bobbin (kg) | 20 | |
Distance from floor to table top (mm) | 995 | |
Machine tool dimensions (W x D x H, mm) | 2,190 x 2,590 x 2,230 | |
Machine tool weight (kg) | 3,400 | |
Total power input | 3-phases 50/60Hz 13KVA | |
External Dimensions (W x D x H) | 775 x 2,250 | |
Weight (Empty) | 450 kg | |
Dielectric fluid | De-ionized Water | |
Capacity | 790 liter | |
Dielectric fluid filtration system | 4 Replaceable paper filters (internal pressure |
Standard Features |
---|
Linear motor (X/Y/U/V axis) |
Absolute linear scales (X/Y/U/V axis) |
Ceramic work-zone |
Remote controller |
3-sided rise and fall work tank |
Improved ease of operation |
Advanced wire tension control |
SPW generator |
SODICK Fine Corner Control |
Energy saving circuit |
Digital PIKA W Plus for super surface finish |
DSF (Dynamic Shape First) |
Automatic water level control |
Fixed Jet AWT (Automatic wire threader) |
Wire end remover |
Dielectric cooling unit |
Voltage stabiliser |
LAN interface |
19“ TFT colour screen |
Intelligent Q3vic EDW |
Anti-virus Software |
USB port |
Work light |
Built-in 20kg wire feeder |
Options |
---|
0.05mm wire spec. |
Esprit CAM software offline (regional option) |
HTP high-voltage circuit |
Automation system |
Taper flex 45 NEO (for taper cutting up to 45°) |
WS4P/5P rotary table (indexing or simultaneous movement) |
L-Cut (Wire chopper) |
8-axis Simultaneous Control (Factory option) |
Anti-Corrosion System (ANCS) |
Booster (Total 60A) |
AL600G "i Groove⁺ Edition" NEW!!
Linear Motor Drive /High speed & High Performance Wire-cut EDM
Newly developed Digital HF control, wire rotation mechanism, energy-saving pump
Manufacturing that is both "High-speed" and "Eco-friendly" that can be changed digitally
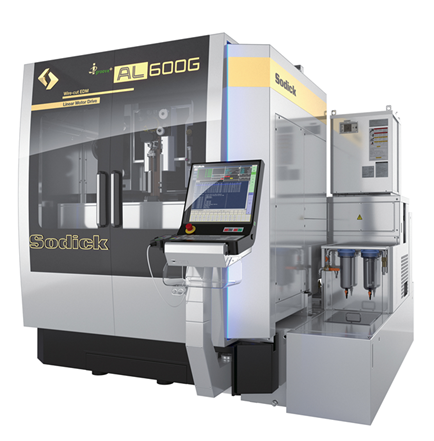
Main Features
4-axis linear motor drive
High-performance linear motors developed and manufactured in-house are used for four axes (XYUV). Precise axis movements without backlash can be maintained semi-permanently.
Demonstrates accurate position control and excellent discharge characteristics while machining, through the high response and high following characteristics which are
the features of the linear motor.
Improved Machining Speed
Newly developed Digital HF control is adopted. By constantly digitally monitoring the status during machining and maintaining optimum discharge conditions, the controller simultaneously
improves machining speed and accuracy. By constantly monitoring the discharge state during machining, stable machining can be maintained at all times, even with changes in water
quality or plate thickness.
Eco-friendly
The wire rotation mechanism (i groove) always performs finish machining with a wear-free wire surface, enabling uniform machining from the top to the bottom of the workpiece.
Reduces wire consumption while reducing streaks and irregularities during finishing of thick workpieces. In addition, a newly developed energy-saving pump system has been adopted
for the dielectric tank, reducing power consumption.
Product Specifications
Technical Specifications | ||
---|---|---|
X - Axis Travel (mm) | 600 | |
Y - Axis Travel (mm) | 400 | |
Z - Axis Travel (mm) | 350 | |
U x V Axis Travel (mm) | 150 x 150 | |
Machining Tank Inner Dimensions W x D (mm) | 1,050 x 710 | |
Max. Taper Angle | ± 25° (Plate Thickness: 130 mm) | |
Max. Workpiece Dimensions W x D x H (mm) | 800 x 570 x 280 (Submerged) 800 x 570 x 340 (Flushing) |
|
Max. Workpiece Weight (kg) | 1,000 | |
Wire Diameter (mm) | ø0.05 - ø0.3 mm *1 | |
Wire Tension (N) | 3 ~ 23 | |
Maximum Wire Feed Rate (mm/sec) | 420 | |
Distance from floor surface to upper surface of table (mm) | 995 | |
Machine Tool Dimensions W x D x H (mm) | 2,575 x 2,945 x 2,345 | |
Machine Installation Dimensions W x D (mm) | 3,860 x 4,245 | |
Total Unit Weight (kg) | 4,600 | |
Total Power Input | 3-phase 50/60 Hz 13 kVA | |
*1 0.05 to 0.1 mm diameters are available as options. |
ALC600G "i Groove Edition"
Smart Linear, Smart Pulse, Premium
First in the world ! Wire Rotation Mechanism "i groove"
Achieving the superlative performance with in-house developed core technologies.
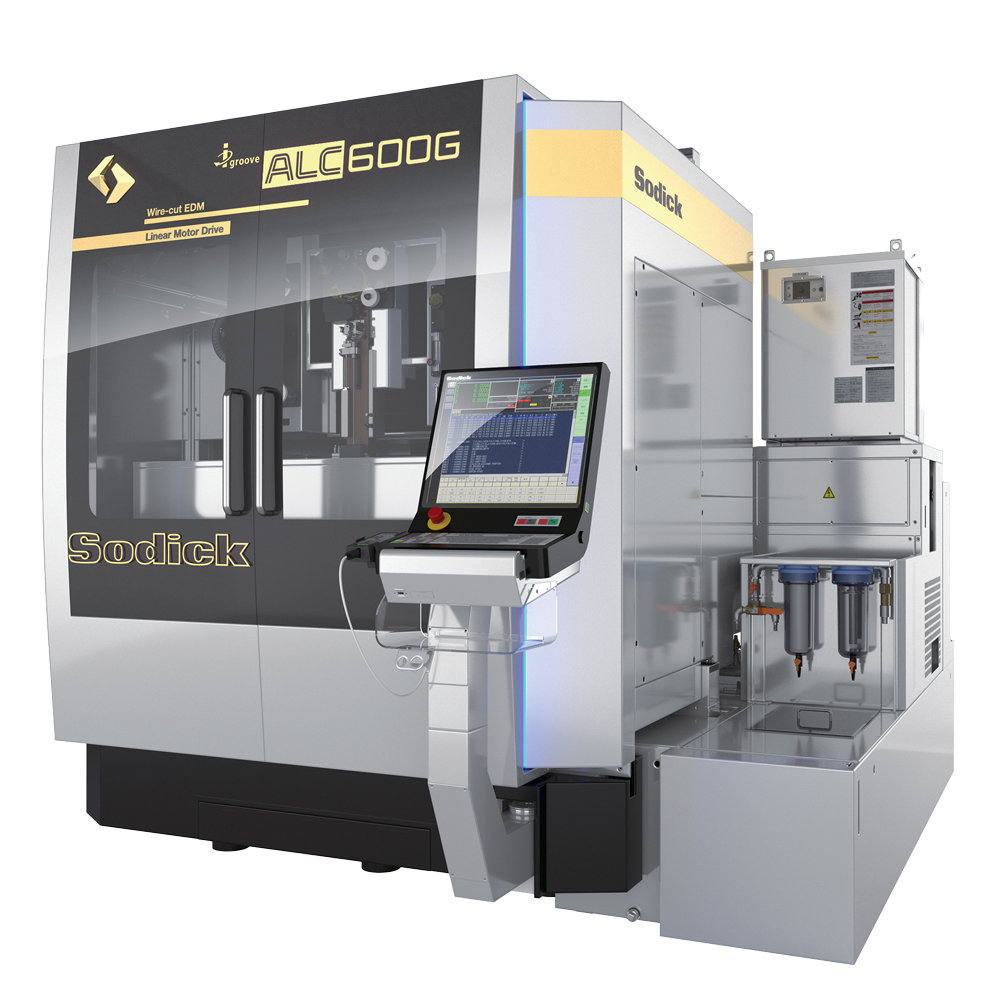
Product Specifications
Technical Specifications | ||
---|---|---|
X/Y/Z axis travel (mm) | 600 x 400 x 350 | |
U/V axis travel (mm) | 150 x 150 | |
Taper angle (Work. height 130mm) | ±25° | |
Work tank dimensions (W x D, mm) | 1050 x 710 | |
Max. workpiece weight (kg) | 1000 | |
Wire diameter (mm) | Ø 0.1 ~ Ø 0.3 | |
Wire tension (N) | 3 ~ 23 | |
Max. wire speed (mm/sec) | 420 | |
Max. wire bobbin (kg) | 20 | |
Distance from floor to table top (mm) | 995 | |
Machine tool dimensions (W x D x H, mm) | 2,575 x 2,945 x 2,345 | |
Machine tool weight (kg) | 4,600 | |
Total power input | 3-phases 50/60Hz 13KVA | |
External Dimensions (W x D x H) | 870 x 2,605 | |
Weight (Empty) | 500 kg | |
Dielectric fluid | De-ionized Water | |
Capacity | 1,000 liter | |
Dielectric fluid filtration system | 4 Replaceable paper filters (internal pressure |
Standard Features |
---|
Linear motor (X/Y/U/V axis) |
Absolute linear scales (X/Y/U/V axis) |
Sodick Motion Controller |
Ceramic work-zone |
Remote controller |
3-sided rise and fall work tank |
Triple filtration system |
Improved ease of operation |
Advanced wire tension control |
SPW generator |
SODICK Fine Corner Control |
Energy saving circuit |
Digital PIKA W Plus for super surface finish |
DSF (Dynamic Shape First) |
Automatic water level control |
Fixed Jet AWT (Automatic wire threader) |
Wire end remover |
Dielectric cooling unit |
Voltage stabiliser |
LAN interface |
19“ TFT colour screen |
Intelligent Q3vic EDW |
Anti-virus Software |
Work light |
Built-in 20kg wire feeder |
Options |
---|
0.05mm wire spec. |
Esprit CAM software offline (regional option) |
HTP high-voltage circuit |
Automation system |
Taper flex 45 NEO (for taper cutting up to 45°) |
WS4P/5P rotary table (indexing or simultaneous movement) |
L-Cut (Wire chopper) |
8-axis Simultaneous Control (Factory option) |
Anti-Corrosion System (ANCS) |
Booster (Total 60A) |
ALN400G "i Groove⁺ Edition" NEW!!
Linear Motor Drive /High speed & High Performance Wire-cut EDM
Newly developed Digital HF control, wire rotation mechanism, energy-saving pump
Manufacturing that is both "High-speed" and "Eco-friendly" that can be changed digitally
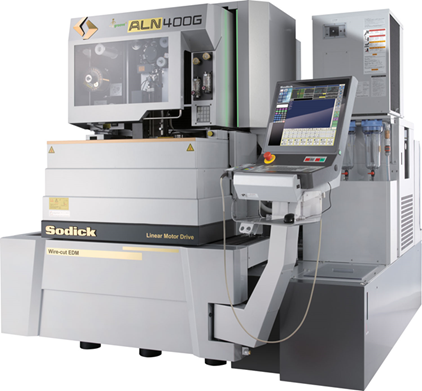
Main Features
4-axis linear motor drive
High-performance linear motors developed and manufactured in-house are used for four axes (XYUV). Precise axis movements without backlash can be maintained semi-permanently.
Demonstrates accurate position control and excellent discharge characteristics while machining, through the high response and high following characteristics which are
the features of the linear motor.
Improved Machining Speed
Newly developed Digital HF control is adopted. By constantly digitally monitoring the status during machining and maintaining optimum discharge conditions, the controller simultaneously
improves machining speed and accuracy. By constantly monitoring the discharge state during machining, stable machining can be maintained at all times, even with changes in water quality
or plate thickness.
Eco-friendly
The wire rotation mechanism (i groove) always performs finish machining with a wear-free wire surface, enabling uniform machining from the top to the bottom of the workpiece.
Reduces wire consumption while reducing streaks and irregularities during finishing of thick workpieces. In addition, a newly developed energy-saving pump system has been adopted
for the dielectric tank, reducing power consumption.
Product Specifications
Technical Specifications | ||
---|---|---|
X - Axis Travel (mm) | 400 | |
Y - Axis Travel (mm) | 300 | |
Z - Axis Travel (mm) | 250 | |
U x V Axis Travel (mm) | 150 x 150 | |
Work Tank Inner Dimensions W x D (mm) | 850 x 610 | |
Max. Taper Angle | ± 25° (Plate Thickness: 130 mm) | |
Max. Workpiece Dimensions W x D x H (mm) | 600 x 470 x 230 (Submerged) 600 x 470 x 240 (Flushing) |
|
Max. Workpiece Weight (kg) | 500 (350 Submerged) | |
Wire Electrode Diameter (mm) | ø0.05 ~ ø0.3 mm *1 | |
Wire Tension (N) | 3 ~ 23 | |
Maximum Wire Feed Rate (mm/sec) | 420 | |
Distance from floor surface to upper surface of table (mm) | 995 | |
Machine Tool Dimensions W x D x H (mm) | 2,190 x 2,425 x 2,205 | |
Machine Installation Dimensions W x D (mm) | 3,440 x 3,660 | |
Total Unit Weight (kg) | 3,200 | |
Total Power Input | 3-phase 50/60 Hz 13 kVA | |
*1 0.05 to 0.1 mm diameters are available as options. |
ALN600G "i Groove⁺ Edition" NEW!!
Linear Motor Drive /High speed & High Performance Wire-cut EDM
Newly developed Digital HF control, wire rotation mechanism, energy-saving pump
Manufacturing that is both "High-speed" and "Eco-friendly" that can be changed digitally
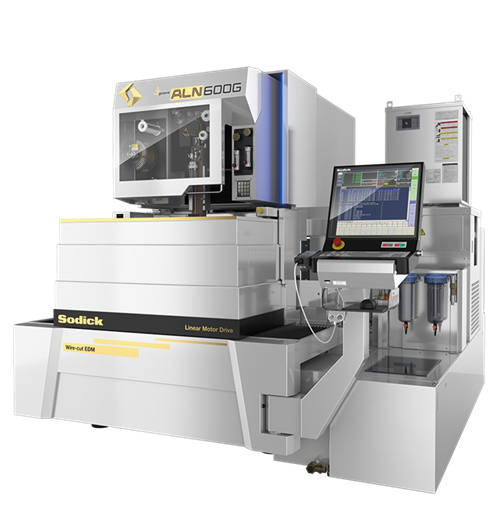
Main Features
4-axis linear motor drive
High-performance linear motors developed and manufactured in-house are used for four axes (XYUV). Precise axis movements without backlash can be maintained semi-permanently.
Demonstrates accurate position control and excellent discharge characteristics while machining, through the high response and high following characteristics which are
the features of the linear motor.
Improved Machining Speed
Newly developed Digital HF control is adopted. By constantly digitally monitoring the status during machining and maintaining optimum discharge conditions, the controller simultaneously
improves machining speed and accuracy. By constantly monitoring the discharge state during machining, stable machining can be maintained at all times, even with changes in water quality
or plate thickness.
Eco-friendly
The wire rotation mechanism (i groove) always performs finish machining with a wear-free wire surface, enabling uniform machining from the top to the bottom of the workpiece.
Reduces wire consumption while reducing streaks and irregularities during finishing of thick workpieces. In addition, a newly developed energy-saving pump system has been adopted
for the dielectric tank, reducing power consumption.
Product Specifications
Technical Specifications | ||
---|---|---|
X - Axis Travel (mm) | 600 | |
Y - Axis Travel (mm) | 400 | |
Z - Axis Travel (mm) | 350 | |
U x V Axis Travel (mm) | 150 x 150 | |
Work Tank Inner Dimensions W x D (mm) | 1,050 x 710 | |
Max. Taper Angle | ± 25° (Plate Thickness: 130 mm) | |
Max. Workpiece Dimensions W x D x H (mm) | 800 x 570 x 280 (Submerged) 800 x 570 x 340 (Flushing) |
|
Max. Workpiece Weight (kg) | 1,000 | |
Wire Electrode Diameter (mm) | ø0.05 ~ ø0.3 mm *1 | |
Wire Tension (N) | 3 ~ 23 | |
Maximum Wire Feed Rate (mm/sec) | 420 | |
Distance from floor surface to upper surface of table (mm) | 995 | |
Machine Tool Dimensions W x D x H (mm) | 2,525 x 2,735 x 2,295 | |
Machine Installation Dimensions W x D (mm) | 3,775 x 4,060 | |
Total Unit Weight (kg) | 4,300 | |
Total Power Input | 3-phase 50/60 Hz 13 kVA | |
*1 0.05 to 0.1 mm diameters are available as options. |
ALN400Q "i Groove Edition" NEW!!
Linear Motor Drive /High Speed & High Precision Wire-cut EDM
First in the world ! Wire Rotation Mechanism "i groove"
Achieving the superlative performance with in-house developed core technologies.
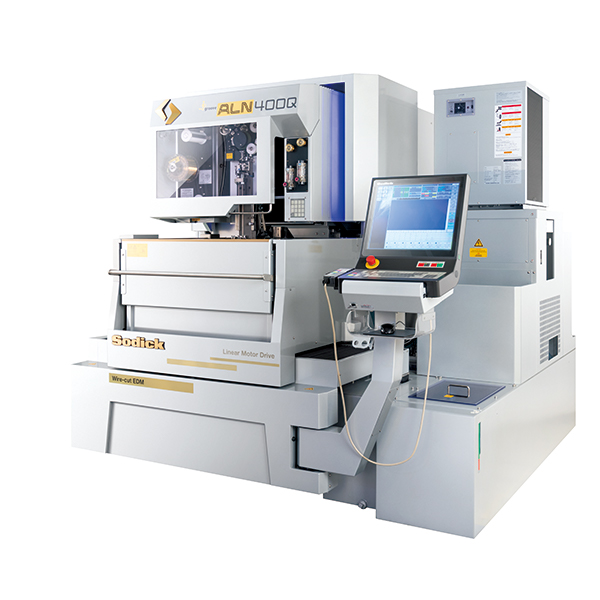
Main Features
More efficient and environmentally friendly finishing of thick plate workpieces.
Wire Rotation Mechanism "i groove"
Applying rotation to the wire during finishing reduces wire consumption and allows a new wire surface to be constantly used for finishing from the top to the bottom of the workpiece.
This is especially suited to finishing thick plate workpieces. It offers innovative machining performance including stable machining dimensions, improvement of surface scoring, and reduced wire consumption.
New groove and step machining function "Stepcut"
It permits machining at the same speed as under standard conditions while significantly improving the accuracy and range of applications when machining shapes with rapidly changing material thickness, such as stepped shapes.
Latest Electrical Discharge Technology for Rapid and Accurate Machining
Sodick has been working for many years to develop the world's best wire-cut electric discharge machines. The AL Series "i Groove Edition" offers flexible control from high peak currents for efficient rough machining to ultra-fine discharge pulses for micro finishing.
In addition, The Sodick linear motor drive is a non-contact system that eliminates the need for ball screws. It is maintenance-free and maintains its initial accuracy almost indefinitely, with no drop off in machine accuracy due to ball screw wear throughout the life of the machine (10 years or more).
Temperature-synchronized machine
All models in the series are equipped as standard with the AIM (AI Maintenance) environmental temperature diagnosis function and TH COM thermal displacement correction function that can handle everything from high-accuracy to rough temperature environments, in addition to a logging function and temperature display of the machine surroundings.
"The newly designed service tank provides a more stable machining environment and improves ease-of-maintenance.
The new service tank has a three-tank structure that completely separates fresh water and the machining fluid after use.
It prevents sludge contamination during machining and provides a more ideal machining environment."
A digital sensor has been newly installed to constantly monitor the filter pressure data and display an alert when filter replacement is necessary.
This allows the operator to machine with confidence and to estimate when filter replacement is due by checking the filter pressure trends on a graph.
Product Specifications
Technical Specifications | |
---|---|
Machining Tank Inner Dimensions (W x D) | 1,050 x 840 mm |
X Axis Travel | 600 mm |
Y Axis Travel | 400 mm |
Z Axis Travel | 350 mm |
U x V Axis Travel | 150 x 150 mm |
Max. Taper Angle | ± 25° (Thickness: 130 mm) |
Max. Workpiece Size (W x D x H) | 800 x 570 x 340 (Flush Machining) mm 800 x 570 x 280 (Immersion Machining) mm |
Max. Weight of Workpiece | 1,000 kg |
Wire Diameter | ø0.1 to ø0.3 mm |
Wire Tension | 3 to 23 N |
Max. Wire Feed Speed | Max. 420 mm/sec |
Distance from Floor to Table Upper Surface | 995 mm |
Total Electric Capacity | 3-phase 50/60 Hz 13 kVA*2 |
External Dimensions (W x D x H) | 870 x 2,605 x 2,179 mm |
Weight (Empty) | 500 kg |
Capacity | 1001 liter |
Machining Fluid Filtration Method | Paper Filter Replacement Type (4 Cylinder Inner Pressure Type) |
Demineralizer | Ion Exchange Resin (18 Liter Specification) |
Max. Machining Current | 40 A (60A : Option) |
Power Supply Input Specification | AC200V 50/60 Hz |
NC Unit | Multi-tasking OS, K-SMC-LINK Method (M4-LINK) |
User’s Memory Capacity | Editing: 100,000 blocks Saving: 30 M bytes |
Memory Device | SSD, Dedicated USB Memory |
Input Method | Dedicated USB Memory, Multi-touch Panel, Keyboard, LAN |
Display Method | 19-inch TFT-LCD |
Printable Characters | Kanji (JIS Level 1 Kanji Characters), Alphabet, Numerical Characters, etc.. |
Keyboard | Standard 101 Keyboard, Function Key |
Position Command Method | Incremental / Absolute in Combination |
Input Range | ±999999.999/±99999.9999 /±9999.99999/±999.999999 (Changeable) |
Electric Discharge Machining Condition | 10,000 conditions can be registered Registration Function (C0000 to C9999) |
Offset Function | 10,000 conditions can be registered (H0000 to H9999) |
Program Sequence Number Specification | Setting from N000000000 to N999999999 |
Coordinate Value | 60 |
Number of Simultaneously Controlled Axes | 4 Axes Max (SPW-E: 8 Axes Max *3) |
Min. Command Unit | 0.001μm |
Min. Drive Unit | 0.01 μm (X, Y, U, V Axes) |
Max. Feed Speed | X, Y-axis: Max. 3 m/min, Z-axis: 2 m/min |
Position Detection Method | Full Closed Loop (Linear Scale) |
Drive System | Linear Motor (X, Y, U, V Axes) |
Drive Mechanism | Linear Motor |
Various Compensation | Pitch Error, Plane Pitch Error, Torque and Torsion Compensation for Each Axis. Workpiece Inclination and Workpiece Distortion Compensation. |
Graphics Function | XY, YZ and XZ Planes, Drawing while Machining, Machining Position, 3-dimensional Machining, Zoom In, Zoom Out, Rotation, Background Drawing, etc. |
The dielectric chillers on Sodick machines contain either
fluorinated greenhouse gas R410A or R407C. *1 Please select the appropriate clamping chuck for your system. · Selection: LN2/LN20. Please consult sales representatives for more details. · Specifications are subject to change without prior notice due to continual research and development. |
ALN600Q "i Groove Edition" NEW!!
Linear Motor Drive /High Performance Wire-cut EDM
First in the world ! Wire Rotation Mechanism "i groove"
Achieving the superlative performance with in-house developed core technologies.
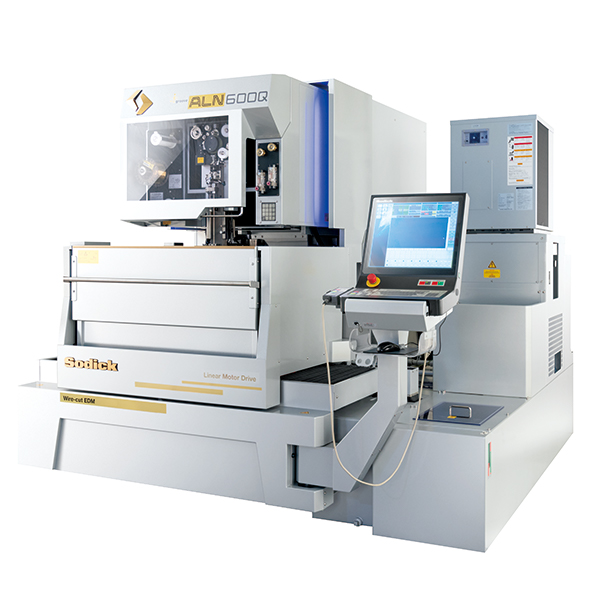
Main Features
More efficient and environmentally friendly finishing of thick plate workpieces.
Wire Rotation Mechanism "i groove"
Applying rotation to the wire during finishing reduces wire consumption and allows a new wire surface to be constantly used for finishing from the top to the bottom of the workpiece.
This is especially suited to finishing thick plate workpieces. It offers innovative machining performance including stable machining dimensions, improvement of surface scoring, and reduced wire consumption.
New groove and step machining function "Stepcut"
It permits machining at the same speed as under standard conditions while significantly improving the accuracy and range of applications when machining shapes with rapidly changing material thickness, such as stepped shapes.
Latest Electrical Discharge Technology for Rapid and Accurate Machining
Sodick has been working for many years to develop the world's best wire-cut electric discharge machines. The AL Series "i Groove Edition" offers flexible control from high peak currents for efficient rough machining to ultra-fine discharge pulses for micro finishing.
In addition, The Sodick linear motor drive is a non-contact system that eliminates the need for ball screws. It is maintenance-free and maintains its initial accuracy almost indefinitely, with no drop off in machine accuracy due to ball screw wear throughout the life of the machine (10 years or more).
Temperature-synchronized machine
All models in the series are equipped as standard with the AIM (AI Maintenance) environmental temperature diagnosis function and TH COM thermal displacement correction function that can handle everything from high-accuracy to rough temperature environments, in addition to a logging function and temperature display of the machine surroundings.
"The newly designed service tank provides a more stable machining environment and improves ease-of-maintenance.
The new service tank has a three-tank structure that completely separates fresh water and the machining fluid after use.
It prevents sludge contamination during machining and provides a more ideal machining environment."
A digital sensor has been newly installed to constantly monitor the filter pressure data and display an alert when filter replacement is necessary.This allows the operator to machine with confidence and to estimate when filter replacement is due by checking the filter pressure trends on a graph.
Product Specifications
Technical Specifications | |
---|---|
Machining Tank Inner Dimensions (W x D) | 1,050 x 840 mm |
X Axis Travel | 600 mm |
Y Axis Travel | 400 mm |
Z Axis Travel | 350 mm |
U x V Axis Travel | 150 x 150 mm |
Max. Taper Angle | ± 25° (Thickness: 130 mm) |
Max. Workpiece Size (W x D x H) | 800 x 570 x 340 (Flush Machining) mm 800 x 570 x 280 (Immersion Machining) mm |
Max. Weight of Workpiece | 1,000 kg |
Wire Diameter | ø0.1 to ø0.3 mm |
Wire Tension | 3 to 23 N |
Max. Wire Feed Speed | Max. 420 mm/sec |
Distance from Floor to Table Upper Surface | 995 mm |
Total Electric Capacity | 3-phase 50/60 Hz 13 kVA*2 |
External Dimensions (W x D x H) | 870 x 2,605 x 2,179 mm |
Weight (Empty) | 500 kg |
Capacity | 1001 liter |
Machining Fluid Filtration Method | Paper Filter Replacement Type (4 Cylinder Inner Pressure Type) |
Demineralizer | Ion Exchange Resin (18 Liter Specification) |
Max. Machining Current | 40 A (60A : Option) |
Power Supply Input Specification | AC200V 50/60 Hz |
NC Unit | Multi-tasking OS, K-SMC-LINK Method (M4-LINK) |
User’s Memory Capacity | Editing: 100,000 blocks Saving: 30 M bytes |
Memory Device | SSD, Dedicated USB Memory |
Input Method | Dedicated USB Memory, Multi-touch Panel, Keyboard, LAN |
Display Method | 19-inch TFT-LCD |
Printable Characters | Kanji (JIS Level 1 Kanji Characters), Alphabet, Numerical Characters, etc.. |
Keyboard | Standard 101 Keyboard, Function Key |
Position Command Method | Incremental / Absolute in Combination |
Input Range | ±999999.999/±99999.9999 /±9999.99999/±999.999999 (Changeable) |
Electric Discharge Machining Condition | 10,000 conditions can be registered Registration Function (C0000 to C9999) |
Offset Function | 10,000 conditions can be registered (H0000 to H9999) |
Program Sequence Number Specification | Setting from N000000000 to N999999999 |
Coordinate Value | 60 |
Number of Simultaneously Controlled Axes | 4 Axes Max (SPW-E: 8 Axes Max *3) |
Min. Command Unit | 0.001 μm |
Min. Drive Unit | 0.01 μm (X, Y, U, V Axes) |
Max. Feed Speed | X, Y-axis: Max. 3 m/min, Z-axis: 2 m/min |
Position Detection Method | Full Closed Loop (Linear Scale) |
Drive System | Linear Motor (X, Y, U, V Axes) |
Drive Mechanism | Linear Motor |
Various Compensation | Pitch Error, Plane Pitch Error, Torque and Torsion Compensation for Each Axis. Workpiece Inclination and Workpiece Distortion Compensation. |
Graphics Function | XY, YZ and XZ Planes, Drawing while Machining, Machining Position, 3-dimensional Machining, Zoom In, Zoom Out, Rotation, Background Drawing, etc. |
*1 Less than ø0.05 mm to ø 0.1 mm is optional.
*2 Electric capacity when ø 0.2 mm wire is used. *3 SPW-E maximum of 8 axis specification is available for AL400P/AL400G/ALN400G, AL600P/AL600G/ALN600G. |
ALN600GH
High-Performance Wire EDM
The ALN600GH features an automatic drop-tank for easy part setup, as well as Sodick’s latest SmartPulse Wire (SPW) Control. Onboard “Intelligent Qvic” programming software is included for easy programming from solid models or dxf files. All Sodick Wire and Sinker EDMs utilize Sodick’s patented Rigid Linear Motor for non-contact axis movement free from friction, wear, and backlash. Since 2006, Sodick machines come with a 10 year positioning accuracy guarantee, ensuring that new ALN machines will maintain the positioning accuracy identified on their factory inspections for the next 10 years.
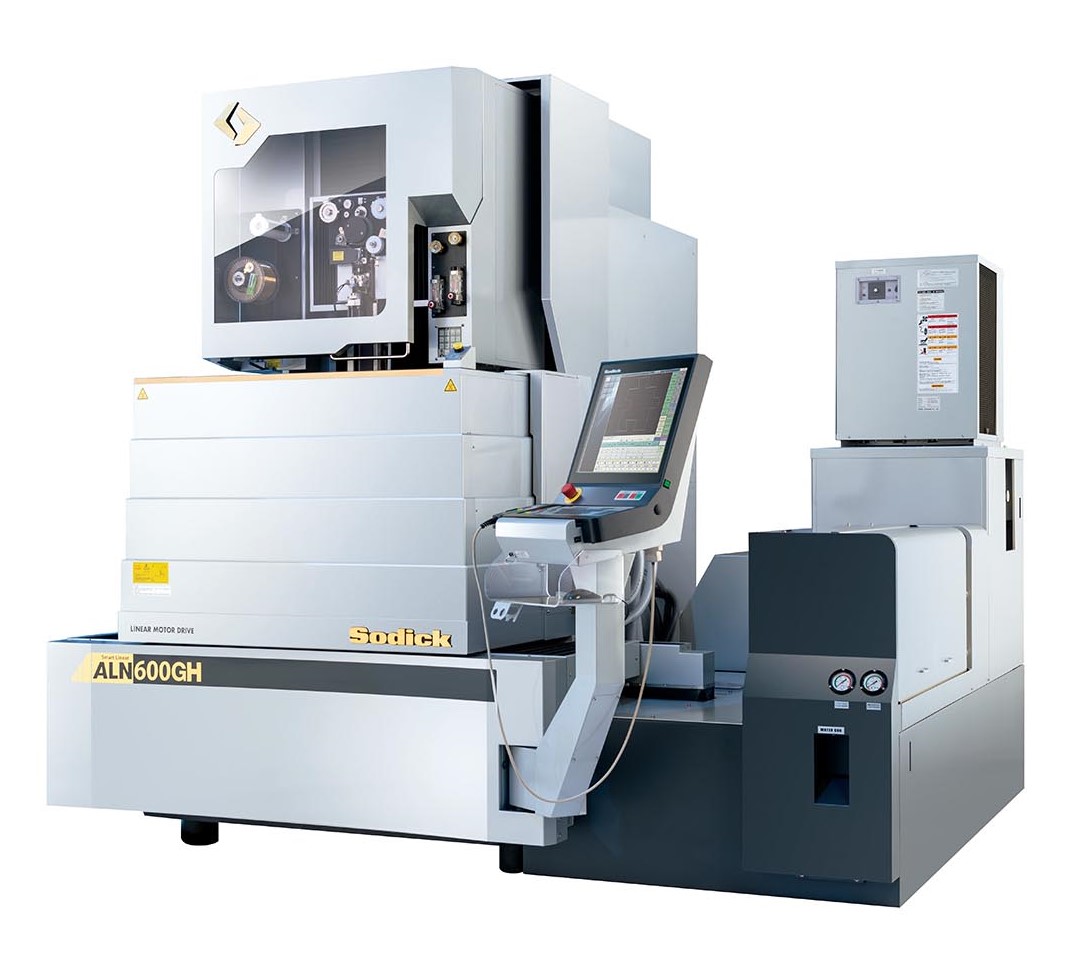
Main Features
Rigid Linear Motor Drives
Sodick’s ALN600GH rigid linear motor driven, high precision Wire EDM machine features increased Z capacity up to nearly 20 inches and new user-friendly EDM technology which further enhances productivity and EDM precision. The machine’s rigid linear motor axes drives are coupled with glass scales on the X, Y, U and V axes which ensure precision cutting and positioning accuracy. Sodick’s X, Y, U and V linear motor drives have no backlash and are backed by Sodick’s 10-Year Positioning Accuracy Guarantee. Sodick currently manufactures and delivers only rigid linear motor driven machines; proving the unrivaled reliability of Sodick's own rigid linear motor technology. Sodick's rigid linear motors have the optimum flat design. The machine castings support the linear motor to achieve ideal linear performance, the ultimate design for precision machining.
CNC Smart Control - SPW
The new Sodick Control SPW (Smart Pulse Wire) has many attractive features, from the use of the industry standard Windows 7 operating system, to an enhanced, 19 inch horizontal TFT multi-touch screen. The ALN control design streamlines the former tablet and classic control modes into a single work screen with easy-access functions. The streamlined design also improves control processing speed, for a highly responsive user experience
The NC programs are supported with 2D and 3D graphics. Maintenance screens show the status of the machine and remote access is possible for maintenance and supervision.
Smart Pulse Generator
The Smart Pulse Generator reduces the number of cuts necessary to achieve the required accuracy and surface finish. This reduction in time translates directly into a financial advantage.
Intelligent Q³vic
Intelligent Q³vic EDW technology allows the importation of 3D CAD files and is standard with the ALN-G Series. This automatic programming system detects the profile of a workpiece that can be machined with Wire EDM and extracts the machining contour. Significant savings in programming hours are possible thanks to this advanced software.
Sodick Motion Controller
The Sodick Motion Controller (K-SMC), accurately controls the high-speed and precise linear motor drive movements through commands from the NC unit. The K-SMC was heavily researched and developed to bring about new technical innovations to electrical discharge machining. Developed in Silicon Valley, CA, the K-SMC accurately controls high-speeds, rapid acceleration and precise positioning.
Product Specifications
Technical Specifications | |
---|---|
X Axis Travel | 600 mm |
Y Axis Travel | 400 mm |
Z Axis Travel | 500 mm |
U x V Axis Travel | 150 x 150 mm |
Wire Diameter Range (min ~ max) | 0.1 ~ 0.3 mm |
Work Tank Dimensions (W x D) | 41.34” x 27.95” (1,050 x 710 mm) |
Maximum Work-piece Weight | 1,000 kg |
Distance From Floor to Table Top | 995 mm |
Machine Tool Dimensions | 2,820 x 2,685 x 2,646 mm |
Machine Weight | 4,500 kg |
Standard Features |
---|
10-Year Positioning Guarantee |
Rigid Linear Motor Drives (X, Y, U and V axes) |
Absolute Linear Scale (X, Y, U and V) |
2 Year Warranty Standard |
SPW (Smart Pulse Wire Control) |
Tablet Style Control Features |
19" LCD Touch Panel Screen |
Smart Pulse Generator |
Digital Pika-W Plus - Super Finishing Circuit |
Advanced Step Machining |
High Precision Positioning Sensor FT-II |
Ceramic Work-Zone |
FJ (Fixed Jet) High Speed AWT |
High Quality Design |
Rigid Cast Construction |
Stable Platform and Environment |
3 Sided Rise/Fall Worktank |
Intelligent Q³vic EDW - Automatic Programming System |
Barrelless Control II |
TMP II Surface Finishing Circuit |
K-SMC Motion Controller |
Three Part Filtration System |
Slide Plate Lubrication |
Advanced Corner Control |
Energy Saving Circuit |
Dielectric Cooling Unit |
Heart NC - CAD-CAM System (on-board) |
Ion-Exchange Unit |
Windows 10 Operating Software Platform |
Automatic Wire Tension Servo Control System |
Automatic Voltage Regulator |
Four Sided Clamping Table |
Z-Axis Automatic Fluid Level Control |
Voltage Booster |
Options |
---|
SPW-E Control - Up to 8 Axis Simultaneous Control - Required for Multi-Axis |
Simultaneous "Turn and Burn" Capability |
Jumbo Wire Feeder 110 lbs (50 kg) |
Integrated 'Jumbo' Wire Feeder 44 lbs (20 kg) |
L-Cut Wire Chopper - Processes Wire for Convenient Storage |
HTP Circuit - High Voltage Circuit that Improves Machining Efficiency when |
Cutting PCD and Similar Materials |
Taper Flex - Hardware and Software to enable the Machining of Precision Taper |
Angles (Up to 22 and 45 Degree Options Available, Contact Sodick for Details) |
UPS (Uninterrupted Power Supply) |
SodickCare +2 or +4 Extended Warranty |
ALC600GH
Smart Linear, Smart Pulse, Premium
Achieving the superlative performance with in-house developed core technologies
Main Features
4-axis linear motor drive
Direct drive method without a ball screw was established, utilizing a high performance linear motor developed and manufactured in-house for the 4 axes of X, Y, U and V. Precise axis movements without backlash can be maintained semi-permanently. Demonstrates accurate position control and excellent discharge characteristics while machining, through the high response and high following characteristics which are the features of the linear motor
New Power Supply Unit & New Machining Circuit
Has a 19-inch horizontal type touch panel, realizing the most up-to-date man-machine interface and also ensuring ease of viewing and ease of use. This machine is standardly equipped with the "barrel-free effect control II" which greatly reduces the barrel amount during machining, and "TMP Control II" which improves the surface roughness of the second cut and realizes high speed finish machining.
Improves Operability and productivity
The operability is improved with the standardly equipped ceramic work stand, square shaped table, automatic three sides up and down type processing tank and Z-axis following automatic liquid level control function. The high speed automatic wire connection unit (FJ-AWT) and the intermediate liquid level control function enables unattended high precision machining can be performed, which improves productivity.
Product Specifications
Technical Specifications | ||
---|---|---|
X/Y/Z axis travel (mm) | 400 x 300 x 250 | |
U/V axis travel (mm) | 150 x 150 | |
Taper angle (Work. height 130mm) | ±25° | |
Work tank dimensions (W x D, mm) | 850 x 610 | |
Max. workpiece weight (kg) | 500 | |
Wire diameter (mm) | Ø 0.1 ~ Ø 0.3 | |
Wire tension (N) | 3 ~ 23 | |
Max. wire speed (mm/sec) | 420 | |
Max. wire bobbin (kg) | 20 | |
Distance from floor to table top (mm) | 995 | |
Machine tool dimensions (W x D x H, mm) | 2,190 x 2,590 x 2,230 | |
Machine tool weight (kg) | 3,400 | |
Total power input | 3-phases 50/60Hz 13KVA | |
External Dimensions (W x D x H) | 775 x 2,250 | |
Weight (Empty) | 450 kg | |
Dielectric fluid | De-ionized Water | |
Capacity | 790 liter | |
Dielectric fluid filtration system | 4 Replaceable paper filters (internal pressure |
|
*1 The diameter of the wire of AWT is φ0.3. |
AL800P NEW!!
Linear Motor Drive /High-speed/Ultra-precision Large-size Wire-cut EDM
Novel Construction and System That Minimize Thermal Displacement.
Achieves Higher-precision and Faster Machining of Large Parts and Molds.

Main Features
4-Axis (XYUV) Linear Motor Drive
High-performance linear motors developed and manufactured by Sodick are adopted for the four XYUV axes. They can maintain accurate axis movement with no backlash semi-permanently, something that is impossible with conventional ball screw drive methods. The high response and high tracking performance that are features of linear motors achieve accurate position control and excellent discharge characteristics during machining.
High Rigidity Construction and Precision Thermal Compensation System
The AL800P adopts a high rigidity construction supported by the ultra-precise roller guide as well as featuring a machining fluid circulation system for major structural components. In addition, a newly developed high-precision thermal compensation system and automatic temperature control by a high-performance inverter cooler minimize the thermal displacement during high-precision machining of large workpieces.
Latest "SPW Power Supply" NC Unit and New Machining Circuits
A variety of the latest technologies for highspeed, high-precision, and high-quality machining, such as Digital-PIKA-W Plus, TMP control II, Barrel-free Effect Control II, new tension servo function, and automatic float control are installed as standard to achieve stable high-efficiency machining with the minimum number of cuts. The horizontal 19-inch touch panel screen offers advanced operability and functionality.
Product Specifications
Technical Specifications | ||
---|---|---|
Work tank inner dimensions W x D (mm) | 1410 x 1110 | |
Axis stroke X x Y x Z (mm) | 800 x 600 x 250 | |
U x V axis travel (mm) | 150 x 150 | |
Max. taper angle | ± 25° (plate thickness: 130 mm) | |
Max. workpiece dimensions (During flushing machining)W x D x H (mm) |
1250 x 1020 x 240 | |
Max. weight of workpiece (During flushing machining)(kg) |
1500 | |
Wire electrode diameter (mm) | 0.1 ~ 0.3 | |
Wire tension (N) | 3 ~ 23 | |
Maximum wire feed rate (mm/sec) | 420 | |
Distance from floor surface to upper surface of table (mm) |
995 | |
Machine tool dimensions W x D x H (mm) | 3300 x 3650 x 2415 | |
Machine installation dimensions W x D (mm) | 4580 x 5050 | |
Total unit weight(kg) | 5750 | |
Total power input | 3-phase, 50/60 Hz, 13 kVA |
AL800G
Linear Motor Drive /High Speed & High Performance/Large-size Wire-cut EDM
Achieving the superlative performance with in-house developed core technologies Advanced Smart Pulse & Advanced Smart Linear
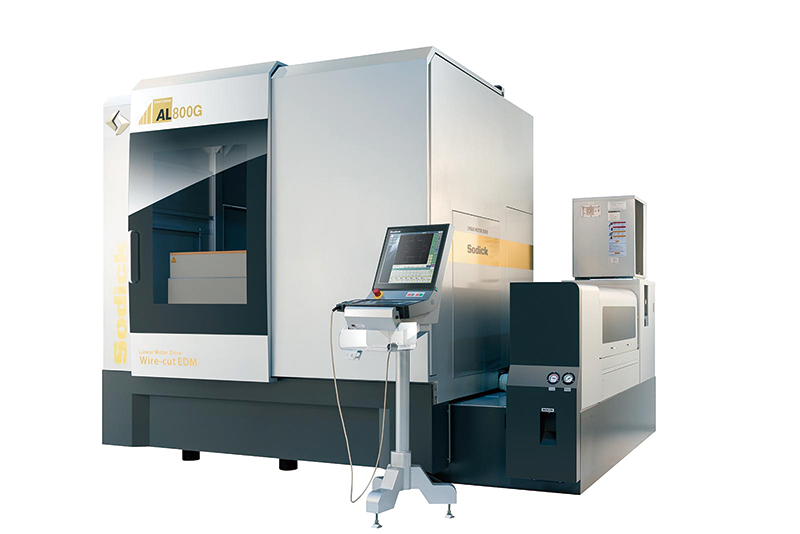
Main Features
4-axis linear motor drive
Direct drive method without a ball screw was established, utilizing a high performance linear motor developed and manufactured in-house for the 4 axes of X, Y, U and V. Precise axis movements without backlash can be maintained semi-permanently. Demonstrates accurate position control and excellent discharge characteristics while machining, through the high response and high following characteristics which are the features of the linear motor
New Power Supply Unit& New Machining Circuit
Providing the improved visibility and operability with the latest man-machine interface achieved by the 19" horizontal touch-panel.This machine is standardly equipped with the "barrel-free effect control Ⅱ" which greatly reduces the barrel amount during machining, and "TMP Control Ⅱ" which improves the surface roughness of the second cut and realizes high speed finish machining.
Large and Thick Workpiece Machining
The AL800G/ALN800G supports a 500mm workpiece thcickness machining standard. It equipped with the automatic vertically sliding door, the "O-shape" work-stand, and ceramics made stand-bases.The high speed automatic wire threading unit (FJ-AWT) and the built-in 20kg wire feeder enables unattended high speed and high precision machining.
Product Specifications
Technical Specifications | ||
---|---|---|
Work tank inner dimensions (W x D) | 1410 x 1110 mm | |
X axis travel | 800 mm | |
Y axis travel | 600 mm | |
Z axis travel | 500 mm | |
U x V axis travel | 200 x 200 mm | |
Max. taper angle | ± 25° (Thickness: 130 mm) | |
Max. workpiece size (W x D x H) | 1250 x 1020 x 500 mm | |
Max. weight of workpiece | 3000 kg | |
Wire diameter | φ 0.1 - φ 0.3 mm | |
Wire tension | 3 - 23 N | |
Wire feed speed Max. | 420 mm/sec | |
Distance from floor to table top | 995 mm | |
Machine tool dimensions (W x D x H)*1 | 3395 x 3640 x 2780 mm | |
Machine installation dimensions (W x D) | 4675 x 5050 mm | |
Machine tool weight*2 | 6000 kg | |
Total power input | 3-phase 50/60 Hz 13 kVA*3 | |
External dimensions (W x D) | 1505 x 3060 mm | |
Weight (empty) | 800 kg | |
Capacity | 1500 liter | |
Filteration method | Replaceable paper filter (Internal pressure 4-cylinder type) |
|
Deionizer | Ion-exchange resin (18 liter) | |
Max. machining current | 40 A ( 60A: Option ) | |
Power requirement | AC200 V 50/60 Hz | |
NC unit | Multi-tasking OS, K-SMC-LINK method (M4-LINK) | |
User memory capacity | Editing: 100,000 blocks, saving: 30MB - |
|
Memory device | SSD, dedicated USB memory | |
Input format | Dedicated USB memory, multi-touch panel, keyboard, LAN |
|
Display type | 19 inch TFT-LCD | |
Character set | Kanji (JIS Level 1 Kanji characters), alphabet, numerical characters, etc. |
|
Keyboard | Standard 101-key, function key | |
Positioning command | Incremental and absolute | |
Max. input command | ±999999.999/±99999.9999/±9999.99999 /±999.999999 (switchable) |
|
Machining conditions storage capacity | 10000 conditions (C0000 - C9999) | |
Offset settings storage capacity | 10000 conditions (H0000 - H9999) | |
Program sequence number assignment | N000000000 to N999999999 | |
Number of coordinates | 60 | |
Simultaneous control axes | Max. 4 axes (SPW-E : Max. 8 axes) | |
Min. command unit | 0.001μm | |
Min. drive unit | 0.01μm (X, Y, U, V axes) | |
Max. feed rate | X, Y axis: max. 3 m/min, Z axis: 2 m/min | |
Position detection | Full closed loop (linear scale) | |
Drive mechanism | Linear motor (X, Y, U, V axes) | |
Compensations | Pitch error compensation, plane pitch error compensation, torque compensation, twist compensation, workpiece alignment compensation, workpiece distortion compensation for each axis |
|
Graphics | XY , YZ , ZX plane, 3D, graphics drawing during machining, enlarge, shrink, rotation, background graphics drawing |
|
*1 Including Power Supply Unit, Dielectric Tank, and Wire Bucket.
*2 Including Power Supply Unit. *3 Electric capacity when a φ 0.2 mm wire is used. |
ALC800G
The Best just got Better: Smart Linear, Smart Pulse
Based on the mindset of "assisting in the product development of customers", Sodick has listened to the demands of customers no matter how insignificant, and has challenged and overcome every difficult technical issue to solve problems. The company has also maintained the stance where Sodick even develop products in-house to solve a problem, if its solution is not available anywhere in the world.
Main Features
NC Unit
Sodick develops and manufactures user-friendly NC units easily operable by anyone, and yet provides supreme machining performance. In order to achieve ultra precision machining, a built-in artificial intelligence is combined with state-of-the-art electrical-discharge machining technologies, which precisely controls the drive system through K-SMC, electrical discharge power supply, and wire running syst
Electrical Discharge Power Supply Unit
The unit contains numerous circuits to optimally control electrical discharge energy. High speed, quality rough cutting essential for finishing is controlled through an optimum discharge pulse to achieve superior surface and form accuracy. The electrical discharge power supply unit containing these circuits is based on energy saving design that works to minimise wasteful energy loss.
Linear Motor
Sodick's linear motor provides high acceleration and positioning accuracy without backlash, by a direct drive mechanism without any single command delay. The excellent dynamic response, stable machining accuracy and its performance does not deteriorate over long periods of operation without any maintenance.
Product Specifications
Technical Specifications | |
---|---|
X Axis travel | 800 mm |
Y Axis travel | 600 mm |
Z Axis travel | 500 mm |
U x V axis travel | 200 x 200 mm |
Taper angle (Work. thickness 130mm) | ±25° |
Work tank dimensions (W x D) | 1,410 x 1,110 mm |
Max. workpiece weight | 3,000 kg |
Wire diameter | 0.1 ~ 0.3 mm |
Wire tension | 3 ~ 23N |
Max. wire speed | 420 mm/sec |
Distance from floor to table top | 995 mm |
Machine tool dimensions (W x D x H) | 3,395 x 3,640 x 2,780 mm |
Machine installation dimensions | 4,675 x 5,050 mm |
Machine tool weight | 6,000 kg |
Total power input | 3-phases 50/60Hz 13KVA |
External dimensions (W x D) | 1505 x 3060 mm |
Weight (empty) | 800 kg |
Capacity | 1500 liter |
Filteration method | Replaceable paper filter (Internal pressure 4-cylinder type) |
Deionizer | Ion-exchange resin (18 liter) |
AL800GH
Linear Motor Drive /High Speed & High Performance/Large-size Wire-cut EDM
Achieving the superlative performance with in-house developed core technologies Advanced Smart Pulse & Advanced Smart Linear
Main Features
4-axis linear motor drive
Direct drive method without a ball screw was established, utilizing a high performance linear motor developed and manufactured in-house for the 4 axes of X, Y, U and V. Precise axis movements without backlash can be maintained semi-permanently. Demonstrates accurate position control and excellent discharge characteristics while machining, through the high response and high following characteristics which are the features of the linear motor
New Power Supply Unit& New Machining Circuit
Providing the improved visibility and operability with the latest man-machine interface achieved by the 19" horizontal touch-panel.
This machine is standardly equipped with the "barrel-free effect control Ⅱ" which greatly reduces the barrel amount during machining, and "TMP Control Ⅱ" which improves the surface roughness of the second cut and realizes high speed finish machining.
Large and Thick Workpiece Machining
The AL800G/ALN800G supports a 500mm workpiece thcickness machining standard. It equipped with the automatic vertically sliding door, the "O-shape" work-stand, and ceramics made stand-bases.
The high speed automatic wire threading unit (FJ-AWT) and the built-in 20kg wire feeder enables unattended high speed and high precision machining.
Product Specifications
Technical Specifications | ||
---|---|---|
Max. workpiece dimensions (W x D x H) | 1,250 x 1,020 x 800(Flushing)mm 1,250 x 1,020 x (Submerged)mm |
|
Max workpiece weight | 3,000 kg | |
Work tank dimensions (W x D) | 1,500 x 1,040 mm | |
X axis travel | 800 mm | |
Y axis travel | 600 mm | |
Z axis travel | 720(80~800) mm | |
U axis x V axis travel | 200 x 200 mm | |
Taper angle (At workpiece thickness of 130mm) |
仮±25° | |
Wire diameter | 仮φ0.1~φ0.3 mm | |
Wire feed speed (max) | 420 mm/sec | |
Wire tension | 3~23 N | |
Machining method | Flushing,Submerged | |
Distance from floor to table top | 1,150 mm | |
Wire bobbin weight | 8 kg | |
Machine dimensions (W x D x H) (Including power supply, supply tank,and wire bucket) |
仮3,300 x 3,500 x 3,400 mm | |
Machine installation space (W x D) | 仮4,580 x 4,950 mm | |
Machine weight (including power supply) | 未 kg | |
Air flow | 0.5 MPa 30 NL/min | |
Total power input | 3-phases 50/60Hz 13 KVA | |
External dimensions (W x D) | 仮1,500x3060 mm | |
Weight (empty) | kg | |
Dielectric tank capacity | 仮2,300 liter | |
Dielectric fluid filtration method | 4 replaceable paper filter (Internal-pressure type) |
|
Deionizer | Ion-exchange resin(18-lit.type) |
ALC800GH
Linear Motor Drive /High Speed & High Performance/Large-size Wire-cut EDM
Achieving the superlative performance with in-house developed core technologies Advanced Smart Pulse & Advanced Smart Linear
Main Features
4-axis linear motor drive
Direct drive method without a ball screw was established, utilizing a high performance linear motor developed and manufactured in-house for the 4 axes of X, Y, U and V. Precise axis movements without backlash can be maintained semi-permanently. Demonstrates accurate position control and excellent discharge characteristics while machining, through the high response and high following characteristics which are the features of the linear motor
New Power Supply Unit& New Machining Circuit
Providing the improved visibility and operability with the latest man-machine interface achieved by the 19" horizontal touch-panel.
This machine is standardly equipped with the "barrel-free effect control Ⅱ" which greatly reduces the barrel amount during machining, and "TMP Control Ⅱ" which improves the surface roughness of the second cut and realizes high speed finish machining.
Large and Thick Workpiece Machining
The AL800G/ALN800G supports a 500mm workpiece thcickness machining standard. It equipped with the automatic vertically sliding door, the "O-shape" work-stand, and ceramics made stand-bases.
The high speed automatic wire threading unit (FJ-AWT) and the built-in 20kg wire feeder enables unattended high speed and high precision machining.
Product Specifications
Technical Specifications | ||
---|---|---|
X Axis travel | 800 mm | |
Y Axis travel | 600 mm | |
Z Axis travel | 730 (80 ~ 810) mm | |
U x V axis travel | 200 x 200 mm | |
Taper angle (Work. thickness 130mm) | ±30° | |
Work tank dimensions (W x D) | 1,312 x 1,058 mm | |
Max. workpiece weight | 3,000 kg | |
Wire diameter | 0.2 ~ 0.3 mm | |
Wire tension | 3 ~ 23N | |
Max. wire speed | 420 mm/sec | |
Distance from floor to table to | 1150 mm | |
Machine tool dimensions (W x D x H) | 4,200 x 3,590 x 3,390 mm | |
Machine installation dimensions | 5,500 x 4,600 mm | |
Machine tool weight | 6,600 kg | |
Total power input | 3-phases 50/60Hz 13KVA | |
External dimensions (W x D) | 2,280 x 3,150 mm | |
Empty weight | 1,100 kg | |
Capacity | 2,500 lit | |
Dielectric fluid filtration system | 4 replaceable paper filter (Internal-pressure type) |
|
Deionizer | Ion-exchange resin (18-lit.type) |
ALN800G
Linear Motor Drive /High Speed & High Performance/Large-size Wire-cut EDM
Achieving the superlative performance
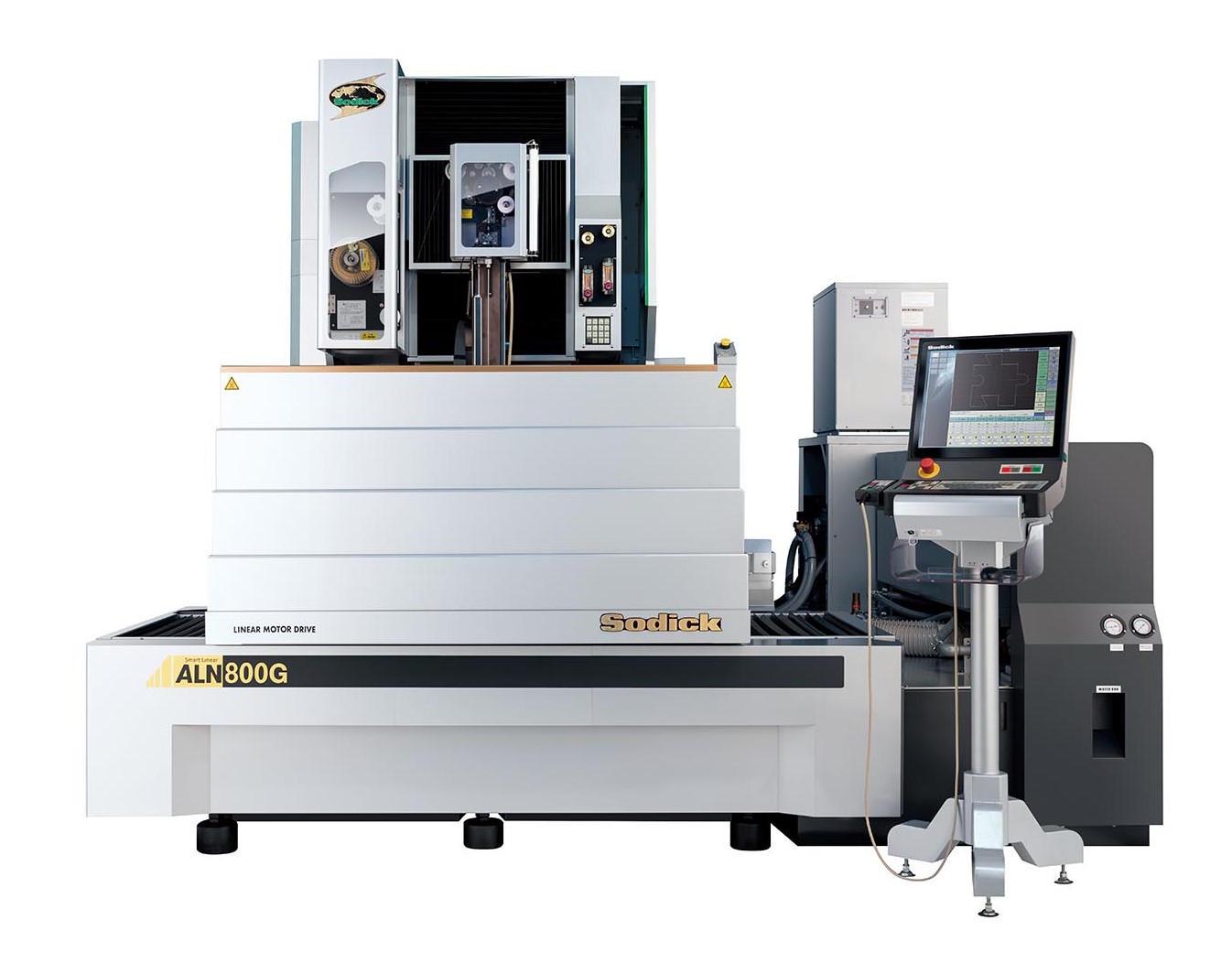
Main Features
4-axis linear motor drive
Direct drive method without a ball screw was established, utilizing a high performance linear motor developed and manufactured in-house for the 4 axes of X, Y, U and V. Precise axis movements without backlash can be maintained semi-permanently. Demonstrates accurate position control and excellent discharge characteristics while machining, through the high response and high following characteristics which are the features of the linear motor.
New Power Supply Unit & New Machining Circuit
Providing the improved visibility and operability with the latest man-machine interface achieved by the 19" horizontal touch-panel.
This machine is standardly equipped with the "barrel-free effect control Ⅱ" which greatly reduces the barrel amount during machining, and "TMP Control Ⅱ" which improves the surface roughness of the second cut and realizes high speed finish machining.
Large and Thick Workpiece Machining
The AL800G/ALN800G supports a 500mm workpiece thcickness machining standard. It equipped with the automatic vertically sliding door, the "O-shape" work-stand, and ceramics made stand-bases. The high speed automatic wire threading unit (FJ-AWT) and the built-in 20kg wire feeder enables unattended high speed and high precision machining.
Product Specifications
Technical Specifications | ||
---|---|---|
Work tank inner dimensions (W x D) | 1410 x 1110 mm | |
X axis travel | 800 mm | |
Y axis travel | 600 mm | |
Z axis travel | 500 mm | |
U x V axis travel | 200 x 200 mm | |
Max. taper angle | ± 25° (Thickness: 130 mm) | |
Max. workpiece size (W x D x H) | 1250 x 1020 x 500 mm | |
Max. weight of workpiece | 3000 kg | |
Wire diameter | φ 0.1 - φ 0.3 mm | |
Wire tension | 3 - 23 N | |
Wire feed speed | Max. 420 mm/sec | |
Distance from floor to table top | 995 mm | |
Machine tool dimensions (W x D x H)*1 | 3310 x 3360 x 2695 mm | |
Machine installation dimensions (W x D) | 4590 x 4760 mm | |
Machine tool weight*2 | 5500 kg | |
Total power input | 3-phase 50/60 Hz 13 kVA*3 | |
External dimensions (W x D) | 1505 x 3060 mm | |
Weight (empty) | 800 kg | |
Capacity | 1500 liter | |
Filteration method | Replaceable paper filter (Internal pressure 4-cylinder type) |
|
Deionizer | Ion-exchange resin (18 liter) | |
Max. machining current | 40 A ( 60A: Option ) | |
Power requirement | AC200 V 50/60 Hz | |
NC unit | Multi-tasking OS, K-SMC-LINK method (M4-LINK) | |
User memory capacity | Editing: 100,000 blocks, saving: 30MB - |
|
Memory device | SSD, dedicated USB memory | |
Input format | Dedicated USB memory, multi-touch panel, keyboard, LAN |
|
Display type | 19 inch TFT-LCD | |
Character set | Kanji (JIS Level 1 Kanji characters), alphabet, numerical characters, etc. |
|
Keyboard | Standard 101-key, function key | |
Positioning command | Incremental and absolute | |
Max. input command | ±999999.999/±99999.9999/±9999.99999 /±999.999999 (switchable) |
|
Machining conditions storage capacity | 10000 conditions (C0000 - C9999) | |
Offset settings storage capacity | 10000 conditions (H0000 - H9999) | |
Program sequence number assignment | N000000000 to N999999999 | |
Number of coordinates | 60 | |
Simultaneous control axes | Max. 4 axes (SPW-E : Max. 8 axes) | |
Min. command unit | 0.001μm | |
Min. drive unit | 0.01μm (X, Y, U, V axes) | |
Max. feed rate | X, Y axis: max. 3 m/min, Z axis: 2 m/min | |
Position detection | Full closed loop (linear scale) | |
Drive mechanism | Linear motor (X, Y, U, V axes) | |
Compensations | Pitch error compensation, plane pitch error compensation, torque compensation, twist compensation , workpiece alignment compensation, workpiece distortion compensation for each axis |
|
Graphics | XY , YZ , ZX plane, 3D, graphics drawing during machining, enlarge, shrink, rotation, background graphics drawing |
|
*1 Including Power Supply Unit, Dielectric Tank, and Wire Bucket.
*2 Including Power Supply Unit. *3 Electric capacity when a φ 0.2 mm wire is used. |
ALN800GH
Linear Motor Drive /High Speed & High Performance/Large-size Wire-cut EDM
Achieving the superlative performance
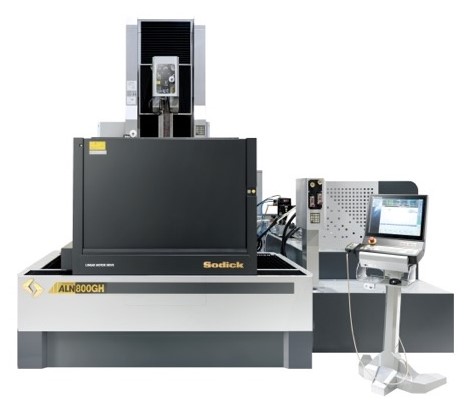
Main Features
4-axis linear motor drive
Direct drive method without a ball screw was established, utilizing a high performance linear motor developed and manufactured in-house for the 4 axes of X, Y, U and V. Precise axis movements without backlash can be maintained semi-permanently. Demonstrates accurate position control and excellent discharge characteristics while machining, through the high response and high following characteristics which are the features of the linear motor.
New Power Supply Unit & New Machining Circuit
Providing the improved visibility and operability with the latest man-machine interface achieved by the 19" horizontal touch-panel.
This machine is standardly equipped with the "barrel-free effect control Ⅱ" which greatly reduces the barrel amount during machining, and "TMP Control Ⅱ" which improves the surface roughness of the second cut and realizes high speed finish machining.
Large and Thick Workpiece Machining
The AL800G/ALN800G supports a 500mm workpiece thcickness machining standard. It equipped with the automatic vertically sliding door, the "O-shape" work-stand, and ceramics made stand-bases. The high speed automatic wire threading unit (FJ-AWT) and the built-in 20kg wire feeder enables unattended high speed and high precision machining.
Product Specifications
Technical Specifications | ||
---|---|---|
Max. workpiece dimensions (W x D x H) | 1,300 x 1,040 x 800 mm | |
Max workpiece weight | 3,000 kg | |
Work tank dimensions (W x D) | 1,312 x 1,058 mm | |
X axis travel | 800 mm | |
Y axis travel | 600 mm | |
Z axis travel (Open height) | 730(80~810) mm | |
U axis x V axis travel | 200 x 200 mm | |
Taper angle (At workpiece thickness of 140mm) |
±30 ° | |
AWT Type | FJ-AWT | |
Upper Guide Type | FJ-AWT Type-A | |
Lower Guide Type | FJ-AWT Type-A | |
Wire diameter | φ0.2~φ0.3 mm | |
Wire feed speed (max) | 420 mm/sec | |
Wire tension | 3~23 N | |
Machining method | Flushing,Submerged | |
Distance from floor to table top | 1,150 mm | |
Wire bobbin weight | Max. weight 20 Kg mm Max. width 220 Kg mm |
|
Machine dimensions (W x D x H) (Including power supply, supply tank,and wire bucket) |
4,120 x 3,500 x 3,365 mm | |
Machine installation space (W x D) | 5,450 x 4,500 mm | |
Machine weight (including power supply and CNT) |
6,600 kg | |
Air flow | 0.5 MPa 30 NL/min |
|
Total power input | 3-phases 50/60Hz 13 KVA | |
External dimensions (W x D) | 2,280x3,150 | |
Weight (empty) | 1,100 kg | |
Dielectric tank capacity | 2,500 liter | |
Dielectric fluid filtration method | 4 replaceable paper filter (Internal-pressure type) |
|
Deionizer | Ion-exchange resin(18-lit.type) | |
*1 The diameter of the wire of AWT is φ0.3. |
VL400Q
Linear Motor Drive /High Speed Wire-cut EDM
Precision parts machining for Medical, Aerospace and Cutting tools The most reliable linear motor driven Wire-cut EDM Improved surface finish supports variety of machining needs
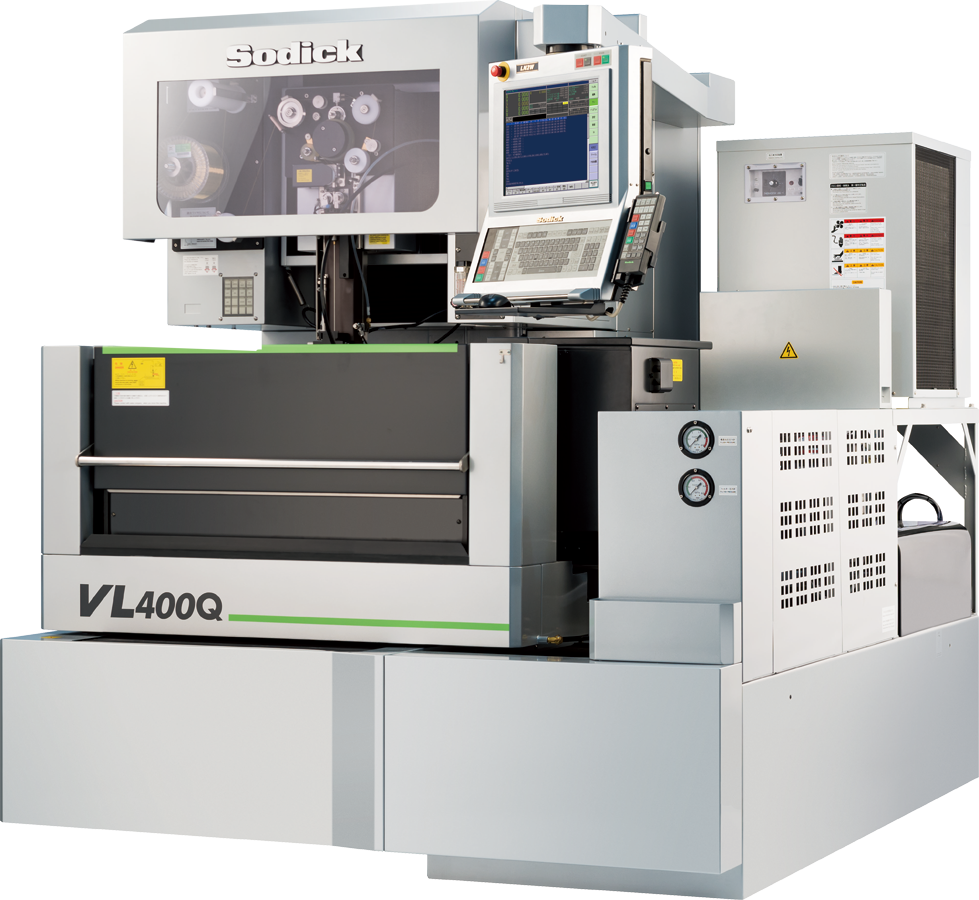
Main Features
No screw drive system
The no screw drive system, which uses a linear motor and linear scale, is the ideal drive method which maintains high-speed and high response semi-permanently. The initial positioning accuracy can be maintained for years and years; machine operators will everlastingly enjoy the remarkably reliable machining performance.
New power supply unit
The new power supply unit employs "Perfect Active Control" technology. It realizes high-speed processing of discharge control and motion control simultaneously. The "Heart-NC", automatic programming system, is installed standard which allows machining program procedure without experience.
Versatility
The VL series are equipped with many advantageous functions as standard; such as, the advanced corner control system, automatic float control, new high quality surface finish circuit, and more. Moreover, Sodick’s in-house made superior ceramics are adopted standard for precision machining.
Product Specifications
Technical Specifications | ||
---|---|---|
Work tank inner dimensions (W x D) | 860 x 690 mm | |
X axis travel | 400 mm | |
Y axis travel | 300 mm | |
Z axis travel | 220 mm | |
U x V axis travel | 80 x 80 mm | |
Max. taper angle | ±15° (Thicnkness 120mm) | |
Max. workpiece size (W x D x H) | 830 x 610 x 215 (Flushing) 830 x 610 x 200 (Submerged) |
|
Max. weight of workpiece | 500 kg (Flushing) 350 kg (Submerged) |
|
Wire diameter | ø0.1 - ø0.3 mm | |
Wire tension | 3 - 23 N | |
Wire feed rate | Max. 420 mm/sec | |
Distance from floor to table top | 900 mm | |
Machine tool dimensions (W x D x H) | 2020 x 2310 x 1990 mm | |
Machine installation area (W x D) | 2700 x 3080 mm | |
Machine tool weight (Including power supply unit) |
2700 kg | |
Total power input | 3-phase 50/60 Hz 11KVA | |
External dimensions (W x D x H) | 755 x 2200 x 1800 mm | |
Weight (empty) | 380 kg | |
Capacity | 590 liter | |
Filteration method | Replaceable paper filter | |
Deionizer | Ion-exchange resin | |
Max. machining current | 32 A | |
Power requirement | 200/220 V 50/60 Hz | |
NC unit | Multi-tasking OS, K-SMC-LINK method | |
User’s memory capacity | Editing: 100,000 blocks、 Saving: 30 MB |
|
Memory device | CF card, dedicated USB memory | |
Input format | Dedicated USB memory, mouse, keyboard, remote controller |
|
Display type | 15 inch TFT-LCD | |
Character set | Alphanumeric and symbols | |
NC unit | Multi-tasking OS, K-SMC-LINK method | |
Positioning command | Incremental and absolute | |
Max. input command | ±999999.999/±99999.9999 /±9999.99999 (switchable) |
|
Machining conditions storage capacity | 1000 conditions (C000 to C999) | |
Offset settings storage capacity | 1000 conditions (H000 to H999) | |
Program sequence number assignment | N000000000 to N999999999 | |
Number of coordinates | 60 | |
Simultaneous control axes | Max. 4 axes | |
Min. input command | 0.1 µm | |
Min. drive unit | 0.1 µm | |
Max. feed rate | Max. 3 m/min | |
Position detection | Full closed loop (linear scale) | |
Drive mechanism | Linear motor | |
Compensations B | acklash and torque compensation (seperated to each axis) |
|
Graphics | XY, YZ, ZX plane, graphics drawing during machining, background graphics drawing |
VL600Q
Linear Motor Drive /High Speed Wire-cut EDM
Precision parts machining for Medical, Aerospace and Cutting tools The most reliable linear motor driven Wire-cut EDM Improved surface finish supports variety of machining needs
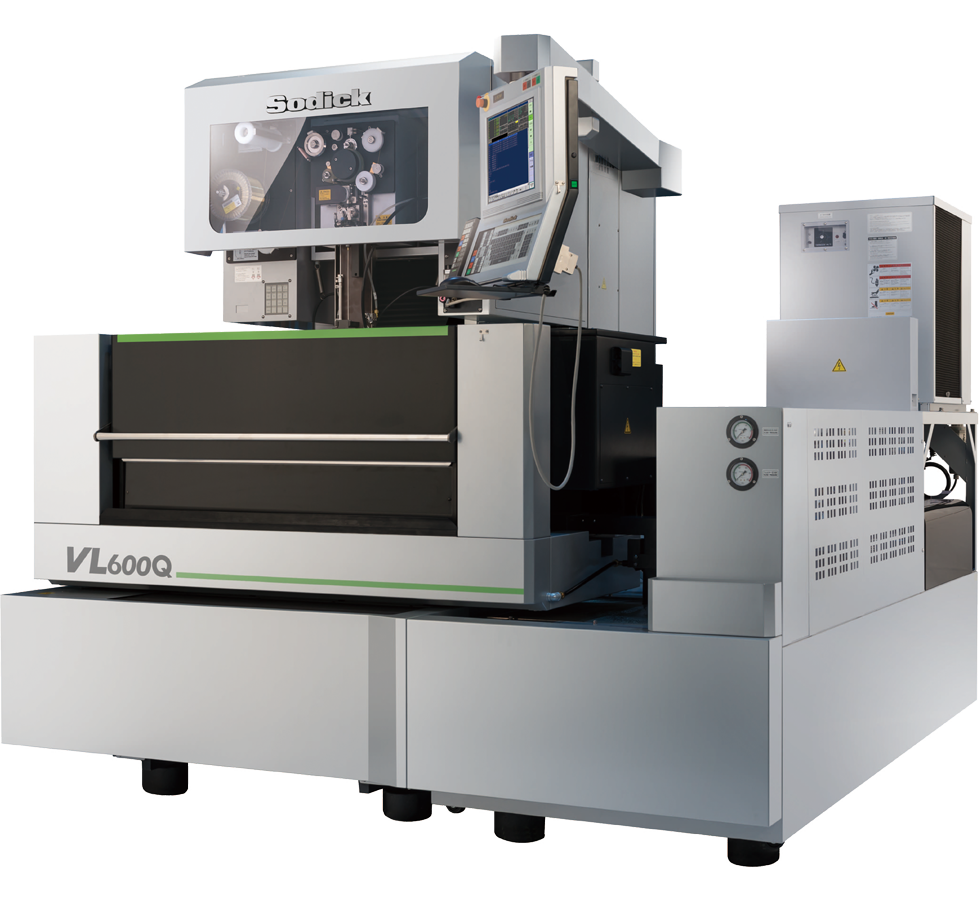
Main Features
Five Core Technologies Developed In-House For Achieving The World's Highest Quality Machining
Starting with the development of electrical discharge circuits, Sodick has continued to make untiring efforts in the research and development of advanced EDMs. Sodick’s philosophy has been the pursuit of the highest level of accuracy, speed and versatility of machining in order to provide the highest quality products to its customers.
Sodick's: Power Supply Units, Discharge Units, Linear Motors, Motion Controllers and Fine Ceramic Components have evolved as its five core technologies. These developments have positioned Sodick at the pinnacle of EDM technologies.
NC Power Supply Unit + Discharge Unit
Sodick’s new VL wire EDM series features Sodick's latest ”LN2W series” power supply unit, which is capable of high-speed, high-precision and high-efficiency machining. The outstanding performance of the LN2W series power supply with 1Gb/sec communication technology “Perfect Active Control” making use of a modern in-house designed NC system running on Windows Operating System. The user interface benefits from a 15” colour screen for ease of use and operation.
Linear Motor
The most outstanding features of the Sodick in-house developed and manufactured Linear Motors are high-speed axis motion and quick response, which result from wear-free motion and without the need for old-fashioned ball screws. Conventional drive systems use ball screws to convert the rotational motion of the motor into the linear motion of the axis stroke, leading to the unavoidable deterioration in the response of high speed servo motors due to back-lash and mechanical lost motion. However linear motors directly provide motion to each axis without converting rotational motion of motor to linear movements.
Ceramic Components
The VL Wire EDM Series benefits from the use of ceramics in critical components such as the upper & lower guide assemblies and worktable supports. Ceramics have a low co-efficient of thermal expansion, light in weight, high in rigidity, resistant to aging and excellent electrical insulation properties, therefore an ideal material for a class leading Wire EDM Machine.
Product Specifications
Technical Specifications | ||
---|---|---|
X x Y x Z axis travel | 600 x 400 x 500 mm | |
U x V axis travel | 90 x 90 mm | |
Work tank dimensions (W x D) | 1,040 x 780 mm | |
Max workpiece weight | 850 kg | |
Taper angle (at workpiece thickness of 120mm) | ±15 ° | |
Wire diameter | ø 0.1 ~ ø 0.3 mm | |
Wire feed speed (max.) | 420 mm/sec | |
Wire tension | 3 ~ 23 N | |
Machining method | Flushing / Submerged | |
Distance from floor to table top | 930 mm | |
Wire bobbin weight | 8 kg | |
Machine dimensions (W x D x H) (including power supply, supply tank) |
3,020 x 2,605 x 2,540 mm | |
Machine installation space (W x D) | 3,700 x 3,395 mm | |
Machine weight (including power supply) |
3,450 kg | |
Air flow | 0.5 MPa, 30 NL/min | |
Total power input | 3-phases 50/60Hz 11 KVA | |
External dimensions (W x D x H) | 1,360 x 2,430 x 1,810 mm | |
Dielectric capacity | 740 kg | |
Required amount | 1,320 l | |
Filtration | 2 replaceable paper filters (internal-pressure type) |
|
Deionizer | Ion-exchange resin (18-lit.type) |
Options |
---|
Sodick Rotary Table (WS4P or WS5P) |
L-Cut Wire Chopper |
44 lb. Wire Spool Feeder |
SodickCare +2 or +4 Extended Warranty |
PCD Tool Cutting Package with ProfDia. |
VL600QH
Linear Motor Drive /High Speed Wire-cut EDM
The VL600QH Wire EDM features Sodick’s Linear Motor Technology. The VL Series is an advanced line of performance Wire EDMs that builds on the technologies of the SL series. The taller VL600QH is well-suited for a wide range of machining applications with even the tallest workpieces.
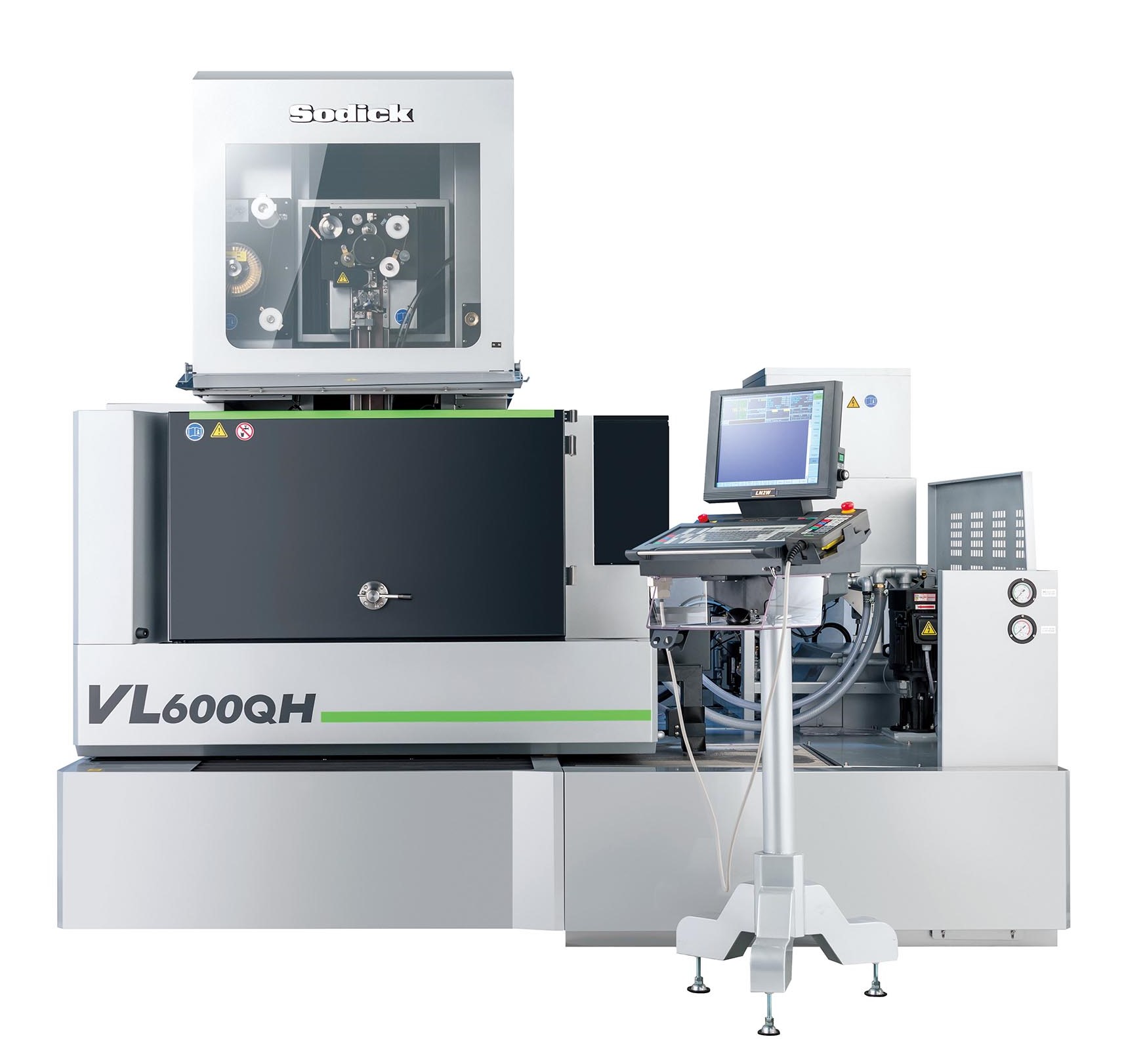
Main Features
No screw drive system
The no screw drive system, which uses a linear motor and linear scale, is the ideal drive method which maintains high-speed and high response semi-permanently. The initial positioning accuracy can be maintained for years and years; machine operators will everlastingly enjoy the remarkably reliable machining performance.
New power supply unit
The new power supply unit employs "Perfect Active Control" technology. It realizes high-speed processing of discharge control and motion control simultaneously. The "Heart-NC", automatic programming system, is installed standard which allows machining program procedure without experience.
Versatility
The VL series are equipped with many advantageous functions as standard; such as, the advanced corner control system, automatic float control, new high quality surface finish circuit, and more. Moreover, Sodick’s in-house made superior ceramics are adopted standard for precision machining.
Product Specifications
Technical Specifications | ||
---|---|---|
Work tank inner dimensions (W x D) | 1040 x 780 mm | |
X axis travel | 600 mm | |
Y axis travel | 400 mm | |
Z axis travel | 270 mm | |
U x V axis travel | 80 x 80 mm | |
Max. taper angle | ±15° (Thicnkness 120mm) | |
Max. workpiece size (W x D x H) | 990 x 670 x 265 (Flushing) 990 x 670 x 250 (Submerged) |
|
Max. weight of workpiece | 500 kg (Flushing) 350 kg (Submerged) |
|
Wire diameter | ø0.1 - ø0.3 mm | |
Wire tension | 3 - 23 N | |
Wire feed rate | Max. 420 mm/sec | |
Distance from floor to table top | 930 mm | |
Machine tool dimensions (W x D x H) | 2620 x 2605 x 2080 mm | |
Machine installation area (W x D) | 3300 x 3395 mm | |
Machine tool weight (Including power supply unit) |
3040 kg | |
Total power input | 3-phase 50/60 Hz 11KVA | |
External dimensions (W x D x H) | 960 x 2430 x 1810 mm | |
Weight (empty) | 420 kg | |
Capacity | 890 liter | |
Filteration method | Replaceable paper filter | |
Deionizer | Ion-exchange resin | |
Max. machining current | 32 A | |
Power requirement | 200/220 V 50/60 Hz | |
NC unit | Multi-tasking OS, K-SMC-LINK method | |
User’s memory capacity | Editing: 100,000 blocks、 Saving: 30 MB |
|
Memory device | CF card, dedicated USB memory | |
Input format | Dedicated USB memory, mouse, keyboard, remote controller |
|
Display type | 15 inch TFT-LCD | |
Character set | Alphanumeric and symbols | |
NC unit | Multi-tasking OS, K-SMC-LINK method | |
Positioning command | Incremental and absolute | |
Max. input command | ±999999.999/±99999.9999 /±9999.99999 (switchable) |
|
Machining conditions storage capacity | 1000 conditions (C000 to C999) | |
Offset settings storage capacity | 1000 conditions (H000 to H999) | |
Program sequence number assignment | N000000000 to N999999999 | |
Number of coordinates | 60 | |
Simultaneous control axes | Max. 4 axes | |
Min. input command | 0.1 µm | |
Min. drive unit | 0.1 µm | |
Max. feed rate | Max. 3 m/min | |
Position detection | Full closed loop (linear scale) | |
Drive mechanism | Linear motor | |
Compensations B | acklash and torque compensation (seperated to each axis) |
|
Graphics | XY, YZ, ZX plane, graphics drawing during machining, background graphics drawing |
VN400Q
Linear Motor Drive /Wire-cut EDM
Supports high-precision component machining and mold machining in the medical and aerospace fields
The entry-class linear motor driven Wire-cut EDM
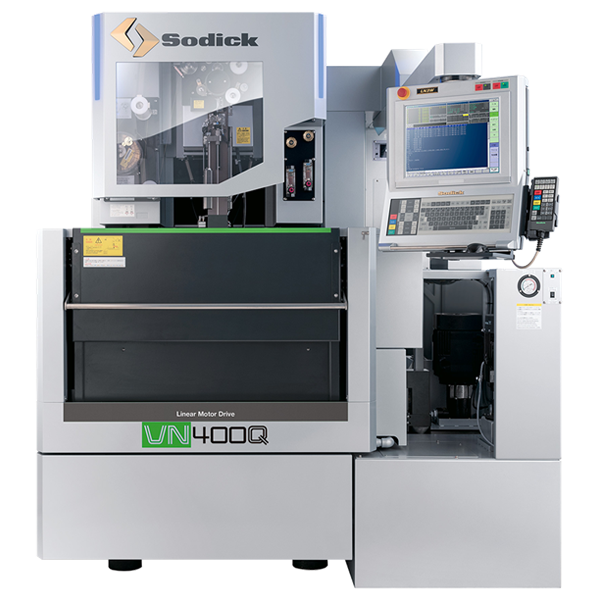
Main Features
Linear Motor Drive System
The no screw drive system, which uses a linear motor and linear scale, is the ideal drive method which maintains high-speed and high response semipermanently.
The initial positioning accuracy can be maintained for years and years; machine operators will everlastingly enjoy the remarkably reliable machining performance.
Upgraded Level of Standard Performance
Sodick's state-of-the-art technologies, such as tension servo functions, automatic wire connection unit, and ceramic stands, are all equipped as standard.
In addition, the machining support system "Heart-NC" allows beginners to easily machine various shapes with a simple programming function.
Faster Machining & Power Consumption Reduction
The new "LN3W/LP3W Power Supply" has resulted in a 5% to 15% increase in floating machining speed compared to the previous model.
In addition, by monitoring the flow rate of the machining fluid and appropriately moving the pump, excess energy is suppressed, resulting in a 20% reduction
in power consumption compared to the previous model.
Product Specifications
Technical Specifications | ||
---|---|---|
X - Axis travel (mm) | 400 | |
Y - Axis travel (mm) | 300 | |
Z - Axis travel (mm) | 230 | |
U x V Axis travel (mm) | 90 x 90 | |
Work Tank Inner Dimensions W x D (mm) | 860 x 740 | |
Max. Taper Angle | ± 15° (Plate Thicnkness : 120mm) | |
Max. Workpiece Dimensions W x D x H (mm) | 830 x 700 x 215 (Submerged) 830 x 700 x 225 (Flushing) |
|
Max. Workpiece Weight (kg) | 500 | |
Wire Electrode Diameter (mm) | ø0.1 - ø0.3 | |
Wire tension (N) | 3 ~ 23 | |
Maximum wire feed rate (mm/sec) | 420 | |
Distance from floor surface to upper surface of table (mm) | 970 | |
Machine Tool Dimensions W x D x H (mm) | 2,070 x 2,920 x 2,135 | |
Machine Installation Dimensions W x D (mm) | 2,750 x 3,785 | |
Total Unit Weight (kg) | 2,920 | |
Total Power Input | 3-phase 50/60Hz 11.5 kVA |
VN600Q
Linear Motor Drive /Wire-cut EDM
Supports high-precision component machining and mold machining in the medical and aerospace fields
The entry-class linear motor driven Wire-cut EDM
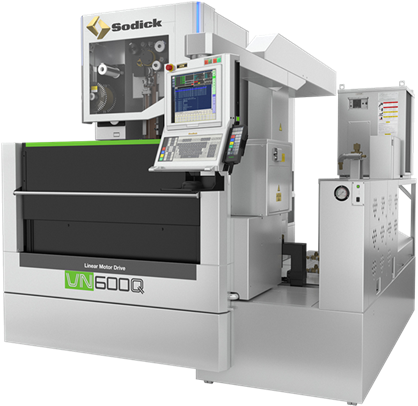
Main Features
Linear Motor Drive System
The no screw drive system, which uses a linear motor and linear scale, is the ideal drive method which maintains high-speed and high response semipermanently.
The initial positioning accuracy can be maintained for years and years; machine operators will everlastingly enjoy the remarkably reliable machining performance.
Upgraded Level of Standard Performance
Sodick's state-of-the-art technologies, such as tension servo functions, automatic wire connection unit, and ceramic stands, are all equipped as standard.
In addition, the machining support system "Heart-NC" allows beginners to easily machine various shapes with a simple programming function.
Faster Machining & Power Consumption Reduction
The new "LN3W/LP3W Power Supply" has resulted in a 5% to 15% increase in floating machining speed compared to the previous model.
In addition, by monitoring the flow rate of the machining fluid and appropriately moving the pump, excess energy is suppressed, resulting in a 20% reduction
in power consumption compared to the previous model.
Product Specifications
Technical Specifications | ||
---|---|---|
X - Axis travel (mm) | 600 | |
Y - Axis travel (mm) | 400 | |
Z - Axis travel (mm) | 310 | |
U x V Axis travel (mm) | 90 x 90 | |
Work Tank Inner Dimensions W x D (mm) | 1,150 x 840 | |
Max. Taper Angle | ± 15° (Plate Thicnkness : 120mm) | |
Max. Workpiece Dimensions W x D x H (mm) | 1,100 x 820 x 295 (Submerged) 1,100 x 820 x 305 (Flushing) |
|
Max. Workpiece Weight (kg) | 850 | |
Wire Electrode Diameter (mm) | ø0.1 - ø0.3 | |
Wire tension (N) | 3 ~ 23 | |
Maximum wire feed rate (mm/sec) | 420 | |
Distance from floor surface to upper surface of table (mm) | 930 | |
Machine Tool Dimensions W x D x H (mm) | 2,620 x 2,605 x 2,080 | |
Machine Installation Dimensions W x D (mm) | 3,300 x 3,395 | |
Total Unit Weight (kg) | 3,040 | |
Total Power Input | 3-phase 50/60Hz 11.5 kVA |
VZ400L
Linear Motor Drive /High Speed Wire-cut EDM
Precision parts machining for Medical, Aerospace and Cutting tools The most reliable linear motor driven Wire-cut EDM Improved surface finish supports variety of machining needs
Main Features
Five Core Technologies Developed In-House For Achieving The World's Highest Quality Machining
Starting with the development of electrical discharge circuits, Sodick has continued to make untiring efforts in the research and development of advanced EDMs. Sodick’s philosophy has been the pursuit of the highest level of accuracy, speed and versatility of machining in order to provide the highest quality products to its customers.
Sodick's: Power Supply Units, Discharge Units, Linear Motors, Motion Controllers and Fine Ceramic Components have evolved as its five core technologies. These developments have positioned Sodick at the pinnacle of EDM technologies.
NC Power Supply Unit + Discharge Unit
Sodick’s new VL wire EDM series features Sodick's latest ”LN2W series” power supply unit, which is capable of high-speed, high-precision and high-efficiency machining. The outstanding performance of the LN2W series power supply with 1Gb/sec communication technology “Perfect Active Control” making use of a modern in-house designed NC system running on Windows Operating System. The user interface benefits from a 15” colour screen for ease of use and operation.
Linear Motor
The most outstanding features of the Sodick in-house developed and manufactured Linear Motors are high-speed axis motion and quick response, which result from wear-free motion and without the need for old-fashioned ball screws. Conventional drive systems use ball screws to convert the rotational motion of the motor into the linear motion of the axis stroke, leading to the unavoidable deterioration in the response of high speed servo motors due to back-lash and mechanical lost motion. However linear motors directly provide motion to each axis without converting rotational motion of motor to linear movements.
Ceramic Components
The VL Wire EDM Series benefits from the use of ceramics in critical components such as the upper & lower guide assemblies and worktable supports. Ceramics have a low co-efficient of thermal expansion, light in weight, high in rigidity, resistant to aging and excellent electrical insulation properties, therefore an ideal material for a class leading Wire EDM Machine.
Product Specifications
Technical Specifications | ||
---|---|---|
Max. workpiece dimensions (W x D x H) | 830 x 610 x 215(Flushing)mm 830 x 610 x 200(Submerged) mm |
|
Max workpiece weight | 500(Flushing)kg 350(Submerged kg |
|
Work tank dimensions (W x D) | 860 x 690 mm | |
X axis travel | 400 mm | |
Y axis travel | 300 mm | |
Z axis travel | 220 mm | |
U axis x V axis travel | 80 x 80 mm | |
Taper angle (At workpiece thickness of 120mm) |
±15 ° | |
Wire diameter | φ0.1~φ0.3 mm | |
Wire feed speed (max) | 420 mm/sec | |
Wire tension | 3~23 N | |
Machining method | Flushing,Submerged | |
Distance from floor to table top | 900 mm | |
Wire bobbin weight | 8 kg | |
Machine dimensions (W x D x H) (including power supply, supply tank) |
2,020 X 2,310 X 1,990 mm | |
Machine installation space (W x D) | 2,700 X 3,080 mm | |
Machine weight (including power supply) |
2,700 kg | |
Air flow | 0.5MPa 30 NL/min |
|
Total power input | 3-phases 50/60Hz 11 KVA | |
External dimensions (W x D x H) | 755 X 2,200 X 1,800 mm | |
Dielectric tank weight | 380 kg | |
Dielectric tank capacity | 590 liter | |
Dielectric fluid filtration method | 2 replaceable paper filter (internal-pressure type) |
|
Deionizer | Ion-exchange resin(18-lit.type) | |
Items | LP2W / LN2W | |
Support 3D Data | Q3vic for EDW (Only LP2W) Parasolid, ACIS, SolidWorks, Solid Edge |
|
Max. machining current | 32A | |
Motion controller | SI-Link | |
Finishing circuit | ALPM / GALPM / NGALPM | |
Power requirement | 3-phases 200V (50 / 60Hz) 11KVA | |
CNC unit | 32 bit CPU | |
User's memory capacity | 30MB | |
Memory device | CF card (4GB), EXT memory (4GB) | |
Input format | EXT memory (4GB) Mouse, Keyboard, Remote controller |
|
Display type | 15.0inch LCD [XGA (1024 x 768)] | |
Character set | Alphanumeric and symbols | |
Keyboard Standard | 101 key base, Function key | |
Positioning command I | ncremental and absolute | |
Max. input command | ±99999.9999 (metric), ±9999.99999 (inch) |
|
Machining conditions storage capacity | 1,000 conditions (C000 ~ C999) | |
Offset setting storage capacity | 1,000 conditions (H000 ~ H999) | |
Program sequence number assignment | N000000000 to N999999999 | |
Subprogram nesting levels | 50 | |
Q command nesting levels | 7 | |
Number of coordinates | 60 | |
Simultaneous control axes | Max. 4 axes | |
Min. input command | 0.1μm | |
Min. drive unit | 0.1μm | |
Jog. feed rate | Max. 3 m/min | |
Control system | Full closed loop (Linear scales) | |
Drive mechanic | Linear motor | |
Compensation | Backlash and Torque compensation (separated to each axes) |
|
Editing | 2-files simultaneous display, Background editing | |
Graphics | XY plane, XY-YZ plane, 3D, Background graphics |
|
Wire tension | Tension servo system | |
Wire feed speed | Max. 25m/min (60Hz) |
VZ600L
Linear Motor Drive /High Speed Wire-cut EDM
Precision parts machining for Medical, Aerospace and Cutting tools The most reliable linear motor driven Wire-cut EDM Improved surface finish supports variety of machining needs
Main Features
Five Core Technologies Developed In-House For Achieving The World's Highest Quality Machining
Starting with the development of electrical discharge circuits, Sodick has continued to make untiring efforts in the research and development of advanced EDMs. Sodick’s philosophy has been the pursuit of the highest level of accuracy, speed and versatility of machining in order to provide the highest quality products to its customers.
Sodick's: Power Supply Units, Discharge Units, Linear Motors, Motion Controllers and Fine Ceramic Components have evolved as its five core technologies. These developments have positioned Sodick at the pinnacle of EDM technologies.
NC Power Supply Unit + Discharge Unit
Sodick’s new VL wire EDM series features Sodick's latest ”LN2W series” power supply unit, which is capable of high-speed, high-precision and high-efficiency machining. The outstanding performance of the LN2W series power supply with 1Gb/sec communication technology “Perfect Active Control” making use of a modern in-house designed NC system running on Windows Operating System. The user interface benefits from a 15” colour screen for ease of use and operation.
Linear Motor
The most outstanding features of the Sodick in-house developed and manufactured Linear Motors are high-speed axis motion and quick response, which result from wear-free motion and without the need for old-fashioned ball screws. Conventional drive systems use ball screws to convert the rotational motion of the motor into the linear motion of the axis stroke, leading to the unavoidable deterioration in the response of high speed servo motors due to back-lash and mechanical lost motion. However linear motors directly provide motion to each axis without converting rotational motion of motor to linear movements.
Ceramic Components
The VL Wire EDM Series benefits from the use of ceramics in critical components such as the upper & lower guide assemblies and worktable supports. Ceramics have a low co-efficient of thermal expansion, light in weight, high in rigidity, resistant to aging and excellent electrical insulation properties, therefore an ideal material for a class leading Wire EDM Machine.
Product Specifications
Technical Specifications | ||
---|---|---|
Max. workpiece dimensions (W x D x H) | 990 x 670 x 265(Flushing)mm 990 x 670 x 250(Submerged) mm |
|
Max workpiece weight | 850(Flushing)kg 700(Submerged kg |
|
Work tank dimensions (W x D) | 1040 x 780 mm | |
X axis travel | 600 mm | |
Y axis travel | 400 mm | |
Z axis travel | 270 mm | |
U axis x V axis travel | 80 x 80 mm | |
Taper angle (At workpiece thickness of 120mm) |
±15 ° | |
Wire diameter | φ0.1~φ0.3 mm | |
Wire feed speed (max) | 420 mm/sec | |
Wire tension | 3~23 N | |
Machining method | Flushing,Submerged | |
Distance from floor to table top | 930 mm | |
Wire bobbin weight | 8 kg | |
Machine dimensions (W x D x H) (including power supply, supply tank) |
2,620 X 2,605 X 2,080 mm | |
Machine installation space (W x D) | 3,300 X 3,395 mm | |
Machine weight (including power supply) |
3,040 kg | |
Air flow | 0.5MPa 30 NL/min |
|
Total power input | 3-phases 50/60Hz 11 KVA | |
External dimensions (W x D x H) | 960 X 2,430 X 1,810 mm | |
Dielectric tank weight | 420 kg | |
Dielectric tank capacity | 890 liter | |
Dielectric fluid filtration method | 2 replaceable paper filter (internal-pressure type) |
|
Deionizer | Ion-exchange resin(18-lit.type) | |
Items | LP2W / LN2W | |
Support 3D Data | Q3vic for EDW (Only LP2W) Parasolid, ACIS, SolidWorks, Solid Edge |
|
Max. machining current | 32A | |
Motion controller | SI-Link | |
Finishing circuit | ALPM / GALPM / NGALPM | |
Power requirement | 3-phases 200V (50 / 60Hz) 11KVA | |
CNC unit | 32 bit CPU | |
User's memory capacity | 30MB | |
Memory device | CF card (4GB), EXT memory (4GB) | |
Input format | EXT memory (4GB) Mouse, Keyboard, Remote controller |
|
Display type | 15.0inch LCD [XGA (1024 x 768)] | |
Character set | Alphanumeric and symbols | |
Keyboard Standard | 101 key base, Function key | |
Positioning command I | ncremental and absolute | |
Max. input command | ±99999.9999 (metric), ±9999.99999 (inch) |
|
Machining conditions storage capacity | 1,000 conditions (C000 ~ C999) | |
Offset setting storage capacity | 1,000 conditions (H000 ~ H999) | |
Program sequence number assignment | N000000000 to N999999999 | |
Subprogram nesting levels | 50 | |
Q command nesting levels | 7 | |
Number of coordinates | 60 | |
Simultaneous control axes | Max. 4 axes | |
Min. input command | 0.1μm | |
Min. drive unit | 0.1μm | |
Jog. feed rate | Max. 3 m/min | |
Control system | Full closed loop (Linear scales) | |
Drive mechanic | Linear motor | |
Compensation | Backlash and Torque compensation (separated to each axes) |
|
Editing | 2-files simultaneous display, Background editing | |
Graphics | XY plane, XY-YZ plane, 3D, Background graphics |
|
Wire tension | Tension servo system | |
Wire feed speed | Max. 25m/min (60Hz) |
AQ750L Premium
Linear Motor Drive Large-Capacity /High Speed Wire-Cut EDM
Direct-drive system, new power supply unit, wire feeder, automatic wire threader, and L-Cut Wire Chopper enables continuous automatic machine operation
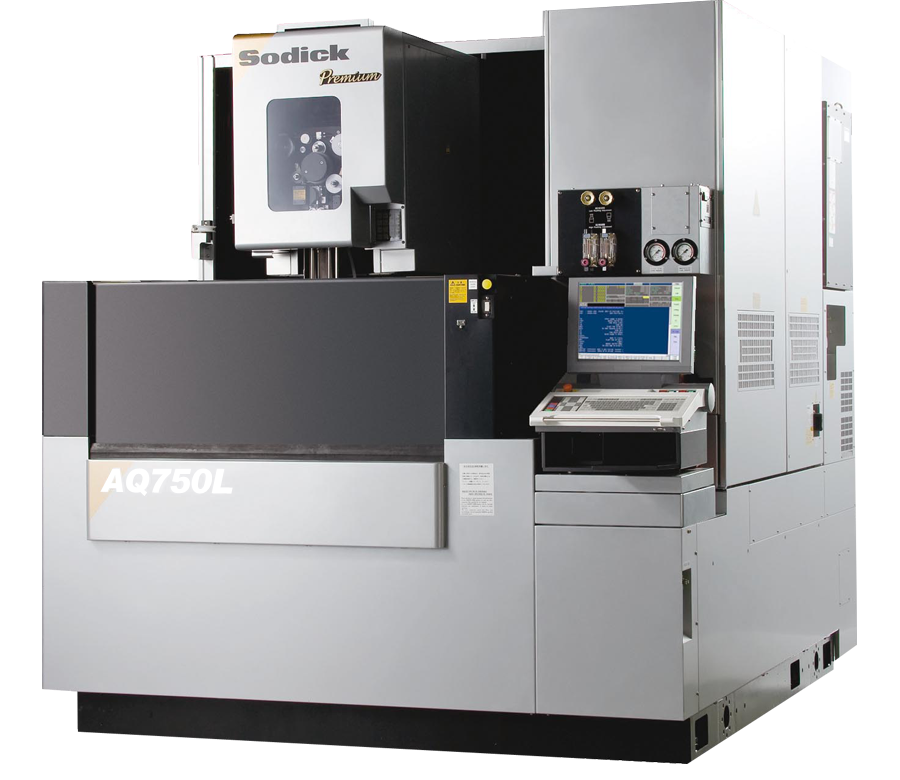
Main Features
Direct-drive & Integrated structure
Sodick's direct-drive system uses linear motors and linear scales, and its excellent positioning accuracy never diminishes over time. The machine also employs a unique integrated structure design, offering the world's best-in-class installation space and machining area size.
Equipped with LP power supply
Significant improvement in operability by employing newly designed, operator-friendly keyboard and remote control. In addition, “Intelligent Q3vic EDW” comes standard, allowing operators to directly send 3D models into the NC unit for practical operation on the work floor.
Ultra-high speed AWT
The Super Jet AWT (Ultra-high speed Automatic Wire Threader unit) uses the conventional pipe-jet method combined with wire annealing function, greatly expanding the range of wire connection modes to choose from and meets the needs of various applications.
Product Specifications
Technical Specifications | |||||||||
---|---|---|---|---|---|---|---|---|---|
Work tank inner dimensions (W x D) | 1264 x 973 mm | ||||||||
X axis stroke | 750 mm | ||||||||
Y axis stroke | 500 mm | ||||||||
Z axis stroke | 400 mm | ||||||||
U x V axis stroke | 770 x 520 mm | ||||||||
|
|
||||||||
Max. workpiece size (W x D x H) | 1050 x 750 x 400 mm | ||||||||
Max. workpiece weight | 1500kg | ||||||||
Wire diameter range | φ0.15-φ0.33 mm * 2 | ||||||||
Wire tension | 3-23 N | ||||||||
Wire feed rate | Max. 420 mm/sec | ||||||||
Distance from floor to table top | 1000 mm | ||||||||
Machine tool dimensions (W x D x H) | 2100 x 2800 x 2350 mm | ||||||||
Machine installation space (W x D) | 3200 x 4100 mm | ||||||||
Machine tool weight | 5300 kg (includes power supply and dielectric tank) |
||||||||
Total power input | 3-phase 50/60 Hz 15 kVA | ||||||||
Capacity | 1265 liter | ||||||||
Filteration method | Replaceable paper filter | ||||||||
Deionizer | Ion-exchange resin (18 liter) | ||||||||
Max. machining current | 60 A | ||||||||
Power requirement | 200 V 50/60 Hz | ||||||||
NC unit | Multi-tasking OS, Si-LINK (Perfect active control) |
||||||||
User memory capacity | Editing: 100,000 blocks、 Saving: 30 MB |
||||||||
Memory device | CF card, external memory | ||||||||
Input format | External memory, touch panel, keyboard, mouse, LAN |
||||||||
Display type | 15 inch TFT-LCD | ||||||||
Character set | Alphanumeric and symbols | ||||||||
Keyboard | Standard 101-key, function keys | ||||||||
Positioning command | Incremental and absolute | ||||||||
Max. input command | ±999999.999/±99999.9999 /±9999.99999 (switchable) |
||||||||
Machining conditions storage capacity | 1000 conditions (C000 to C999) | ||||||||
Offset settings storage capacity | 1000 conditions (H000 to H999) | ||||||||
Program sequence number assignment | N000000000 to N999999999 | ||||||||
Number of coordinates | 60 | ||||||||
Simultaneous control axes | Max. 4 axes (LP20WH: 6/8 axes) | ||||||||
Min. input command | 0.001 µm | ||||||||
Min. drive unit | 0.01 µm | ||||||||
Max. feed rate | X, Y axis: max. 3 m/min, Z axis: 2 m/min | ||||||||
Position detection | Combination of full-closed (linear scale) and semi-closed loop control |
||||||||
Drive mechanism | Combination of linear and rotary motor | ||||||||
Compensations | Pitch error compensation, plane pitch error compensation, torque compensation for each axis |
||||||||
Graphics | XY, YZ, ZX plane, graphics drawing during machining, background graphics drawing |
||||||||
*1 Only the jet nozzle needs to be replaced.
*2 Maximum wire diameter for AWT (Automatic Wire Threader) is φ0.3 mm |
|||||||||
Please consult with your local sales representative for more details. |
AQ900L Premium
Linear Motor Drive Large-Capacity /High Speed Wire-Cut EDM
Direct-drive system, new power supply unit, wire feeder, automatic wire threader, and L-Cut Wire Chopper enables continuous automatic machine operation
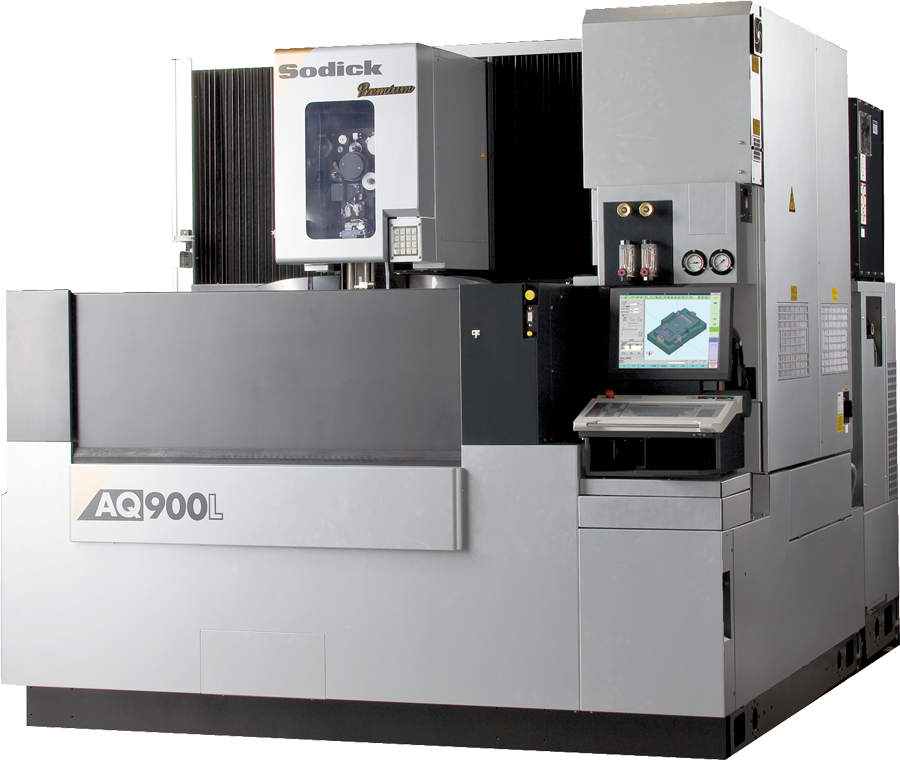
Main Features
Direct-drive & Integrated structure
Sodick's direct-drive system uses linear motors and linear scales, and its excellent positioning accuracy never diminishes over time. The machine also employs a unique integrated structure design, offering the world's best-in-class installation space and machining area size.
Equipped with LP power supply
Significant improvement in operability by employing newly designed, operator-friendly keyboard and remote control. In addition, “Intelligent Q3vic EDW” comes standard, allowing operators to directly send 3D models into the NC unit for practical operation on the work floor.
Ultra-high speed AWT
The Super Jet AWT (Ultra-high speed Automatic Wire Threader unit) uses the conventional pipe-jet method combined with wire annealing function, greatly expanding the range of wire connection modes to choose from and meets the needs of various applications.
Product Specifications
Technical Specifications | |||||||||
---|---|---|---|---|---|---|---|---|---|
Work tank inner dimensions (W x D) | 1374 x 1133 mm | ||||||||
X axis stroke | 900 mm | ||||||||
Y axis stroke | 600 mm | ||||||||
Z axis stroke | 400 mm | ||||||||
U x V axis stroke | 920 x 620 mm | ||||||||
|
|
||||||||
Max. workpiece size (W x D x H) | 1200 x 900 x 400 mm | ||||||||
Max. workpiece weight | 2000kg | ||||||||
Wire diameter range | φ0.15-φ0.33 mm * 2 | ||||||||
Wire tension | 3-23 N | ||||||||
Wire feed rate | Max. 420 mm/sec | ||||||||
Distance from floor to table top | 1050 mm | ||||||||
Machine tool dimensions (W x D x H) | 2380 x 3150 x 2395 mm | ||||||||
Machine installation space (W x D) | 3500 x 4200 mm | ||||||||
Machine tool weight | 8000 kg (includes power supply and dielectric tank) |
||||||||
Total power input | 3-phase 50/60 Hz 15 kVA | ||||||||
Capacity | 1600 liter | ||||||||
Filteration method | Replaceable paper filter | ||||||||
Deionizer | Ion-exchange resin (18 liter) | ||||||||
Max. machining current | 60 A | ||||||||
Power requirement | 200 V 50/60 Hz | ||||||||
NC unit | Multi-tasking OS, Si-LINK (Perfect active control) |
||||||||
User memory capacity | Editing: 100,000 blocks、 Saving: 30 MB |
||||||||
Memory device | CF card, external memory | ||||||||
Input format | External memory, touch panel, keyboard, mouse, LAN |
||||||||
Display type | 15 inch TFT-LCD | ||||||||
Character set | Alphanumeric and symbols | ||||||||
Keyboard | Standard 101-key, function keys | ||||||||
Positioning command | Incremental and absolute | ||||||||
Max. input command | ±999999.999/±99999.9999 /±9999.99999 (switchable) |
||||||||
Machining conditions storage capacity | 1000 conditions (C000 to C999) | ||||||||
Offset settings storage capacity | 1000 conditions (H000 to H999) | ||||||||
Program sequence number assignment | N000000000 to N999999999 | ||||||||
Number of coordinates | 60 | ||||||||
Simultaneous control axes | Max. 4 axes (LP20WH: 6/8 axes) | ||||||||
Min. input command | 0.001 µm | ||||||||
Min. drive unit | 0.01 µm | ||||||||
Max. feed rate | X, Y axis: max. 3 m/min, Z axis: 2 m/min | ||||||||
Position detection | Combination of full-closed (linear scale) and semi-closed loop control |
||||||||
Drive mechanism | Combination of linear and rotary motor | ||||||||
Compensations | Pitch error compensation, plane pitch error compensation, torque compensation for each axis |
||||||||
Graphics | XY, YZ, ZX plane, graphics drawing during machining, background graphics drawing |
||||||||
*1 Only the jet nozzle needs to be replaced.
*2 Maximum wire diameter for AWT (Automatic Wire Threader) is φ0.3 mm |
|||||||||
Please consult with your local sales representative for more details. |
AQ1200L
Linear Motor Drive Large-Capacity /High Speed Wire-Cut EDM
Direct-drive system, new power supply unit, wire feeder, automatic wire threader, and L-Cut Wire Chopper enables continuous automatic machine operation
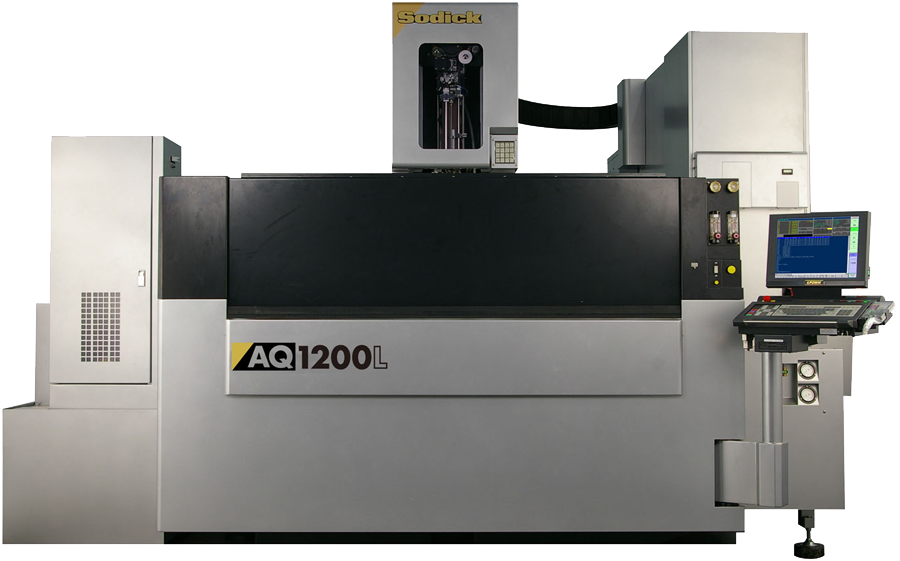
Main Features
Direct-drive & Integrated structure
Sodick's direct-drive system uses linear motors and linear scales, and its excellent positioning accuracy never diminishes over time. The machine also employs a unique integrated structure design, offering the world's best-in-class installation space and machining area size.
Equipped with LP power supply
Significant improvement in operability by employing newly designed, operator-friendly keyboard and remote control. In addition, “Intelligent Q3vic EDW” comes standard, allowing operators to directly send 3D models into the NC unit for practical operation on the work floor.
Ultra-high speed AWT
The Super Jet AWT (Ultra-high speed Automatic Wire Threader unit) uses the conventional pipe-jet method combined with wire annealing function, greatly expanding the range of wire connection modes to choose from and meets the needs of various applications.
Product Specifications
Technical Specifications | |||||||||
---|---|---|---|---|---|---|---|---|---|
Work tank inner dimensions (W x D) | 1824 x 1400 mm | ||||||||
X axis stroke | 1200 mm | ||||||||
Y axis stroke | 800 mm | ||||||||
Z axis stroke | 400 mm | ||||||||
U x V axis stroke | 1220 x 820 mm | ||||||||
|
|
||||||||
Max. workpiece size (W x D x H) | 1600 x 1200 x 400 mm | ||||||||
Max. workpiece weight | 4000kg | ||||||||
Wire diameter range | φ0.15-φ0.33 mm * 2 | ||||||||
Wire tension | 3-23 N | ||||||||
Wire feed rate | Max. 420 mm/sec | ||||||||
Distance from floor to table top | 1200 mm | ||||||||
Machine tool dimensions (W x D x H) | 4100 x 3870 x 2490 mm | ||||||||
Machine installation space (W x D) | 5200 x 5200 mm | ||||||||
Machine tool weight | 11000 kg (includes power supply and dielectric tank) |
||||||||
Total power input | 3-phase 50/60 Hz 15 kVA | ||||||||
Capacity | 3000 liter | ||||||||
Filteration method | Replaceable paper filter | ||||||||
Deionizer | Ion-exchange resin (18 liter) | ||||||||
Max. machining current | 60 A | ||||||||
Power requirement | 200 V 50/60 Hz | ||||||||
NC unit | Multi-tasking OS, Si-LINK (Perfect active control) |
||||||||
User memory capacity | Editing: 100,000 blocks、 Saving: 30 MB |
||||||||
Memory device | CF card, external memory | ||||||||
Input format | External memory, touch panel, keyboard, mouse, LAN |
||||||||
Display type | 15 inch TFT-LCD | ||||||||
Character set | Alphanumeric and symbols | ||||||||
Keyboard | Standard 101-key, function keys | ||||||||
Positioning command | Incremental and absolute | ||||||||
Max. input command | ±999999.999/±99999.9999 /±9999.99999 (switchable) |
||||||||
Machining conditions storage capacity | 1000 conditions (C000 to C999) | ||||||||
Offset settings storage capacity | 1000 conditions (H000 to H999) | ||||||||
Program sequence number assignment | N000000000 to N999999999 | ||||||||
Number of coordinates | 60 | ||||||||
Simultaneous control axes | Max. 4 axes (LP20WH: 6/8 axes) | ||||||||
Min. input command | 0.001 µm | ||||||||
Min. drive unit | 0.01 µm | ||||||||
Max. feed rate | X, Y axis: max. 3 m/min, Z axis: 2 m/min | ||||||||
Position detection | Combination of full-closed (linear scale) and semi-closed loop control |
||||||||
Drive mechanism | Combination of linear and rotary motor | ||||||||
Compensations | Pitch error compensation, plane pitch error compensation, torque compensation for each axis |
||||||||
Graphics | XY, YZ, ZX plane, graphics drawing during machining, background graphics drawing |
||||||||
*1 Only the jet nozzle needs to be replaced.
*2 Maximum wire diameter for AWT (Automatic Wire Threader) is φ0.3 mm |
|||||||||
Please consult with your local sales representative for more details. |
AQ1500L
Linear Motor Drive Large-Capacity /High Speed Wire-Cut EDM
Direct-drive system, new power supply unit, wire feeder, automatic wire threader, and L-Cut Wire Chopper enables continuous automatic machine operation
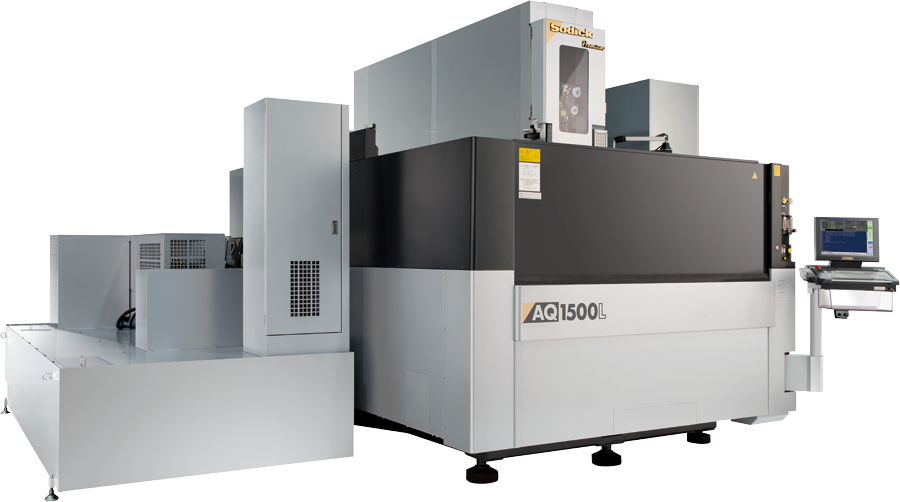
Main Features
Direct-drive & Integrated structure
Sodick's direct-drive system uses linear motors and linear scales, and its excellent positioning accuracy never diminishes over time. The machine also employs a unique integrated structure design, offering the world's best-in-class installation space and machining area size.
Equipped with LP power supply
Significant improvement in operability by employing newly designed, operator-friendly keyboard and remote control. In addition, “Intelligent Q3vic EDW” comes standard, allowing operators to directly send 3D models into the NC unit for practical operation on the work floor.
Ultra-high speed AWT
The Super Jet AWT (Ultra-high speed Automatic Wire Threader unit) uses the conventional pipe-jet method combined with wire annealing function, greatly expanding the range of wire connection modes to choose from and meets the needs of various applications.
Product Specifications
Technical Specifications | |||||||||
---|---|---|---|---|---|---|---|---|---|
Work tank inner dimensions (W x D) | 2124 x 1600 mm | ||||||||
X axis stroke | 1500 mm | ||||||||
Y axis stroke | 1000 mm | ||||||||
Z axis stroke | 600 mm | ||||||||
U x V axis stroke | 1520 x 1020 mm | ||||||||
|
|
||||||||
Max. workpiece size (W x D x H) | 1900 x 950 x 600 mm | ||||||||
Max. workpiece weight | 8000kg | ||||||||
Wire diameter range | φ0.15-φ0.33 mm * 2 | ||||||||
Wire tension | 3-23 N | ||||||||
Wire feed rate | Max. 420 mm/sec | ||||||||
Distance from floor to table top | 1200 mm | ||||||||
Machine tool dimensions (W x D x H) | 5600 x 4435 x 2930 mm | ||||||||
Machine installation space (W x D) | 6700 x 5765 mm | ||||||||
Machine tool weight | 15000 kg (includes power supply and dielectric tank) |
||||||||
Total power input | 3-phase 50/60 Hz 15 kVA | ||||||||
Capacity | 3000 liter | ||||||||
Filteration method | Replaceable paper filter | ||||||||
Deionizer | Ion-exchange resin (18 liter) | ||||||||
Max. machining current | 60 A | ||||||||
Power requirement | 200 V 50/60 Hz | ||||||||
NC unit | Multi-tasking OS, Si-LINK (Perfect active control) |
||||||||
User memory capacity | Editing: 100,000 blocks、 Saving: 30 MB |
||||||||
Memory device | CF card, external memory | ||||||||
Input format | External memory, touch panel, keyboard, mouse, LAN |
||||||||
Display type | 15 inch TFT-LCD | ||||||||
Character set | Alphanumeric and symbols | ||||||||
Keyboard | Standard 101-key, function keys | ||||||||
Positioning command | Incremental and absolute | ||||||||
Max. input command | ±999999.999/±99999.9999 /±9999.99999 (switchable) |
||||||||
Machining conditions storage capacity | 1000 conditions (C000 to C999) | ||||||||
Offset settings storage capacity | 1000 conditions (H000 to H999) | ||||||||
Program sequence number assignment | N000000000 to N999999999 | ||||||||
Number of coordinates | 60 | ||||||||
Simultaneous control axes | Max. 4 axes (LP20WH: 6/8 axes) | ||||||||
Min. input command | 0.001 µm | ||||||||
Min. drive unit | 0.01 µm | ||||||||
Max. feed rate | X, Y axis: max. 3 m/min, Z axis: 2 m/min | ||||||||
Position detection | Combination of full-closed (linear scale) and semi-closed loop control |
||||||||
Drive mechanism | Combination of linear and rotary motor | ||||||||
Compensations | Pitch error compensation, plane pitch error compensation, torque compensation for each axis |
||||||||
Graphics | XY, YZ, ZX plane, graphics drawing during machining, background graphics drawing |
||||||||
*1 Only the jet nozzle needs to be replaced.
*2 Maximum wire diameter for AWT (Automatic Wire Threader) is φ0.3 mm |
|||||||||
Please consult with your local sales representative for more details. |
AP250L (Oil)
Linear Motor Drive /Precision Wire-cut EDM
Improved productivity in the superfine and super-precision screw-less drive and new power supply unit
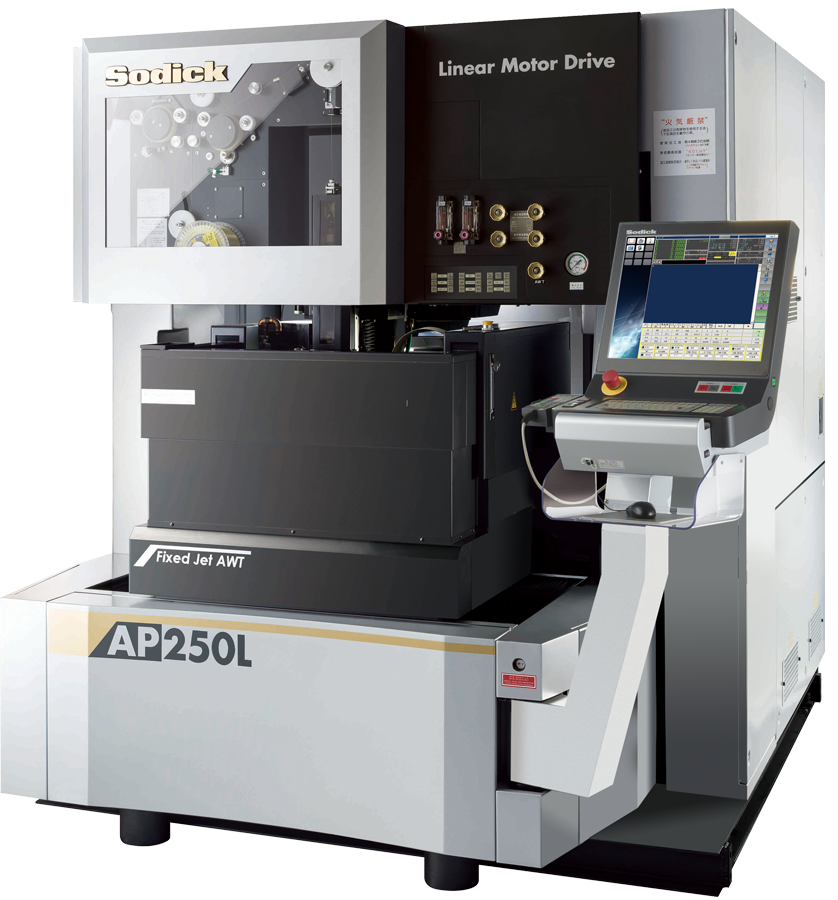
Main Features
Screw-less drive + gantry type construction
This machine uses a linear motor drive which realizes high speed and fast response and also a low center of gravity gantry-type column, enabling the mechanical displacement due to mass motion to be reduced to the minimum possible, and also realizing greatly improved positioning and machining accuracy.
Newly developed power supply unit
The new power supply unit employs 5th generation EDM "Perfect Active Control" technology. It also uses 1 Gbit/sec serial communication technology, realizing high-speed processing of discharge control and motion control simultaneously.
Improved workability and operability
This machine comes with a three-sided automated vertical sliding machining tank, a U-shaped work stand, and other parts, resulting in greatly improved workability during setup process. In addition, the operation panel is separate from the machine, which enables all work to be performed from the front of the machine.
Product Specifications
Technical Specifications | ||
---|---|---|
X axis travel | 250 mm | |
Y axis travel | 150 mm | |
Z axis travel | 120 mm | |
U x V axis travel 35 x 35 mm | ||
Max. taper angle | ± 7° (Thickness: 100 mm) | |
Max. workpiece size (W x D x H) | 400 x 270 x 100 mm | |
Max. weight of workpiece | 80 kg | |
Wire diameter | φ0.03 - φ0.2 mm (Optional : φ0.03 mm) | |
Wire tension | 3 - 18 N | |
Wire feed speed | Max. 250 mm/sec | |
Distance from floor to table top | 1080 mm | |
Machine tool dimensions (W x D x H) | 1860 x 2515 x 2105 mm (includes a power supply and service tank) |
|
Machine tool weight | 3730 kg (includes a power supply and service tank) |
|
Total power input | 3-phase 50/60 Hz 10 kVA | |
Machine tool dimensions (W x D x H) | 1050 x 1310 x 1600 mm | |
Machining fluid | Electric Discharge Machining Oil (4th class 3rd petroleum class) |
|
Capacity | 375 liter | |
Method of filtering machining | fluid Replaceable paper filter | |
Max. machining current | 40 A | |
Power requirement | AC 200V 50/60 H z | |
NC unit | Multi-tasking OS, K-SMC-LINK method (M4-LINK) |
|
User memory capacity | Editing: 100,000 blocks Saving: 30MB |
|
Memory device | SSD, external memory | |
Input format | External memory, touch panel, keyboard, LAN |
|
Display type | 19 inch TFT-LCD | |
Character set | Alphanumeric and symbols | |
Keyboard | Standard Software 101-key, function key |
|
Positioning command | Incremental and absolute | |
Max. input command | ±999999.999/±99999.9999/ ±9999.99999 (switchable) |
|
Machining conditions storage capacity | 10000 conditions (C0000 to C9999) | |
Offset settings storage capacity | 10000 conditions (H0000 to H9999) | |
Program sequence number assignment | N000000000 to N999999999 | |
Number of coordinates | 60 | |
Simultaneous control axes | Max. 4 axes (SPW-E : Max. 8 axes) | |
Min. command unit | 0.001µm | |
Min. drive unit | 0.01µm | |
Max. feed rate | X, Y axis: max. 3 m/min, Z axis: 2 m/min | |
Position detection | Full closed loop (linear scale) | |
Drive mechanism | Linear motor (X, Y, U, V Axes) | |
Compensations | Pitch error compensation, plane pitch error compensation, torque compensation, twist compensation, workpiece alignment compensation for each axis |
|
Graphics | XY, YZ, ZX plane, graphics drawing during machining, enlarge, shrink, rotation, background graphics drawing |